Buen dia a todos. Les traigo a mi atención mi versión de la alteración del módulo del pedal del volante para una computadora para controlar herramientas eléctricas.
La idea era usar el módulo del pedal en el diseño, el resto del volante roto por los niños para la computadora (tal vez el resto del volante también funcionará, no lo tiré). Como hay dos pedales en el módulo, decidí hacer dos canales de control independientes. El primer canal tiene una función de carga de encendido / apagado. El segundo canal tiene la función de controlar suavemente la potencia de carga hasta que se apaga por completo.
En este diseño se utilizó:
- Módulo de pedal del volante GW-10VR para computadora.
- Dimmer chino 220v 2kW.
- Enchufe RO1 RA10-002 - 2 piezas.
- Cable de alimentación con enchufe.
- Microinterruptor tipo RWA-401 - 2 piezas
- Prensaestopas PG-7.
- Sujetadores M3, M4.
- Chatarra de plástico.
De las herramientas utilizadas:
- Taladro.
- MFI tipo "Dremel".
- Soldador.
- Pistola termo-pegamento.
- Tijeras para metal.
- Destornilladores, cortadores de alambre, etc.
El módulo de pedal fue solo un hallazgo, porque En su diseño, tiene una solución de engranaje lista para usar, desde los pedales hasta el eje de resistencia variable.
En el diseño, la resistencia variable fue reemplazada por 500 kOhm (era 50 kOhm). Como se encontró una resistencia variable adecuada con solo un eje redondo en el alijo, tuve que moler el chaflán. Se inserta una cuña de plástico en el corte.
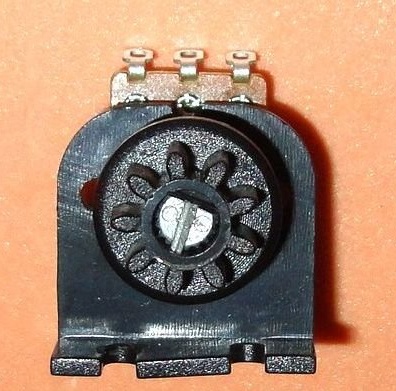
Por lo general, en mis diseños uso mis propios atenuadores, que están hechos para las características de diseño del producto. Aquí decidí usar un atenuador chino prefabricado (estuve inactivo durante mucho tiempo) que tenía que estar ligeramente "aligerado", porque él trabaja en modo pulsado y trabaja con una herramienta eléctrica que tiene su propio electronica bloques de ajuste, el circuito de corrección R1-C1 solo interfiere. Se produce un sobrecalentamiento de la resistencia R1 (probado en la práctica). Por lo tanto, R1 y C1 se eliminaron del tablero. La pasta termoconductora KPT-8 se aplicó al radiador (inicialmente completamente ausente).
La numeración de las partes en el diagrama corresponde a su numeración indicada en la pizarra.
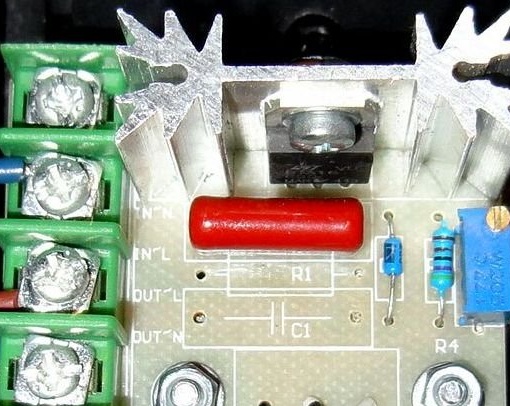
Los microinterruptores se fijan en la carcasa con tornillos M3.
Las placas de metal están montadas en pedales con tornillos M3.
Después de instalar los pedales en la carcasa, las placas se ajustaron en su lugar.
Dado que los enchufes van más allá de las dimensiones de la caja, para protegerlos de los desechos, el panel posterior fue cortado de plástico blando para ellos.
La base de las salidas se fija a la caja con tornillos M4.Una entrada de cable está instalada en el centro.
El cable de red se conecta a través de la regleta de terminales (para reemplazarlo fácilmente). Los microinterruptores se conectan mediante conectores de cuchilla, se usan los contactos que se cierran cuando se presiona el botón. Porque el recorrido completo del pedal no proporciona la rotación máxima del eje de resistencia variable, luego, cuando está montado en la carcasa, el engranaje está montado de modo que cuando el pedal está completamente pisado hay un valor de resistencia máximo (500 kOhm). Con el pedal completamente presionado, la resistencia es de 27 kΩ. Este rango es suficiente para el funcionamiento normal. Hubo una idea de conectar un interruptor de láminas en paralelo con la resistencia variable R5, y conectar un imán a los pedales, estableciendo la distancia de respuesta con el pedal completamente presionado. Pero hasta ahora no tengo necesidad de esto. El desplazamiento del rango de ajuste con la resistencia de sintonización R4 es suficiente.
Los cables de alimentación se unen con bridas de plástico, el cable de la resistencia variable se fija con adhesivo termofusible. Esto evitó la sujeción de los cables durante el montaje de la carcasa.
Los cables de alimentación se unen con bridas de plástico, el cable de la resistencia variable se fija con adhesivo termofusible. Esto evitó la sujeción de los cables durante el montaje de la carcasa.
En la parte inferior del cuerpo tuvo que cortar agujeros. No permiten que las placas de metal en los pedales descansen contra la parte inferior del cuerpo cuando los pedales están completamente presionados. Como resultado, los pedales descansan únicamente en los topes de goma en la parte superior del cuerpo. Al mismo tiempo, las placas de metal no alcanzan un poco el borde exterior de la parte inferior del cuerpo (por 1-1.5 mm).
La placa del atenuador se fija a la parte inferior de la carcasa a través de juntas de fibra de vidrio en los tornillos M3. Los topes de plástico para la cubierta del atenuador están hechos de plástico blando con un grosor de 8 mm y están pegados al cuerpo con superpegamento (empotrado en 3 mm). La cubierta está cortada de plástico blando de 3 mm de espesor. La tapa se atornilla con cuatro tornillos pequeños a los topes. Los orificios en la parte inferior de la caja están sellados con cinta de reparación (tal vez más tarde, sellaré con plástico delgado).
El zócalo del primer canal está conectado al cable de red a través de un microinterruptor. El zócalo del segundo canal está conectado al cable de red a través de un atenuador y un microinterruptor, lo que garantiza su desconexión completa de la red con el pedal completamente presionado.
El funcionamiento del atenuador en este diseño se probó en las siguientes herramientas eléctricas:
- Lijadora de banda Hammer LSM800 (800W - sin controlador de velocidad incorporado).
- Pistola pulverizadora de compresor Bosch PFS 3000-2 (650W - sin controlador de velocidad incorporado)
- Taladro Makita HP1621F (650W - controlador de velocidad incorporado).
- Taladro Makita DP2010 (370W - controlador de velocidad incorporado).
- MFI tipo "Dremel" Top Machine DM-130B (135W - controlador de velocidad incorporado)
- El motor para la máquina de coser TUR 2 (90W - recto, sin pedal), se requiere un ligero ajuste del rango de ajuste de la resistencia R4.
En instrumentos equipados con arrancadores suaves incorporados y (o) electrónica constante no se probó.
A 800 W, el disipador térmico solo se calienta ligeramente. Creo que con una carga de 1400-1500 W necesitará un radiador más grande. Para las herramientas disponibles (las tengo hasta 1000W), y lo suficiente.
El diseño resultó ser especialmente conveniente cuando se utilizan taladros instalados en el soporte de taladro. Y cuando se utiliza una rectificadora montada sobre una mesa. Controle convenientemente el soplador para enfriar las piezas durante la soldadura. Porque Ambas manos son libres.
Debido a las almohadillas de goma (patas) y al hecho de que el talón del pie está en el soporte, el dispositivo no se mueve en el piso. En general, estaba satisfecho con las capacidades operativas del dispositivo. Más tiempo lo dirá.
Si falta algo en la descripción, espero que estos matices puedan considerarse en las fotos enviadas. Pido disculpas de antemano por posibles errores y errores tipográficos.
Si necesita información adicional, escriba a la oficina de correos, intentaré asegurarme de responder. Comentarios, ideas, sugerencias para mejorar el diseño y comentarios son bienvenidos.
El diseño resultó ser especialmente conveniente cuando se utilizan taladros instalados en el soporte de taladro. Y cuando se utiliza una rectificadora montada sobre una mesa. Controle convenientemente el soplador para enfriar las piezas durante la soldadura. Porque Ambas manos son libres.
Debido a las almohadillas de goma (patas) y al hecho de que el talón del pie está en el soporte, el dispositivo no se mueve en el piso. En general, estaba satisfecho con las capacidades operativas del dispositivo. Más tiempo lo dirá.
Si falta algo en la descripción, espero que estos matices puedan considerarse en las fotos enviadas. Pido disculpas de antemano por posibles errores y errores tipográficos.
Si necesita información adicional, escriba a la oficina de correos, intentaré asegurarme de responder. Comentarios, ideas, sugerencias para mejorar el diseño y comentarios son bienvenidos.
Noviembre 2019