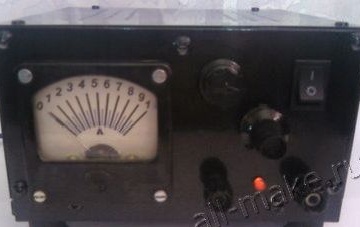
Todos tienen un descanso diferente en su tiempo libre. A alguien le gusta acostarse en el sofá, alguien va al gimnasio y el autor de esto hecho en casa, basado en sus necesidades, habilidades y capacidades, decidió usar su tiempo libre para crear un nuevo cargador universal a partir de herramientas improvisadas que estaban en su taller.
Materiales y herramientas utilizados para crear un cargador universal:
vivienda de una fuente de alimentación de computadora
taladro
línea
marcador
Cable PDDSKT de 1,6 mm de diámetro
alambre de cobre con un diámetro de 2.2 mm
resina epoxi
voltímetro
impresora para imprimir escala amperimétrica
transformador de la serie TS-180
tiristor KU202N
pasta térmica
un par de radiadores
transistores kt315, kt361
imprimación para metal
Resistencia variable de 33 kΩ
hoja de fibra de vidrio de doble cara
-pintura
Consideremos con más detalle la descripción del dispositivo creado y las etapas de su ensamblaje.
El objetivo principal del trabajo casero era la idea de crear un cargador universal, es decir, uno que pudiera cargar casi todas las baterías disponibles en el hogar: desde baterías de microcadmio de dedo pequeño hasta baterías de plomo-ácido para automóviles. Naturalmente, la idea de tal dispositivo está lejos de ser nueva, y existen muchos esquemas diferentes para su creación, uno de los cuales el autor decidió darle vida en uno de sus días libres.
Por lo tanto, se decidió hacer un cargador simple pero universal, cuya corriente de carga se puede ajustar continuamente desde los valores más bajos hasta el máximo requerido a 10 A, que estará limitado solo por el voltaje disponible en la salida del transformador.
Paso uno: preparar la carcasa del dispositivo.
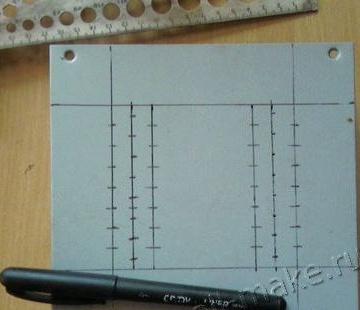
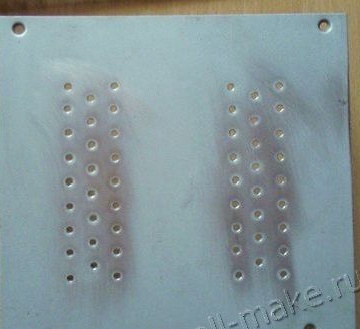
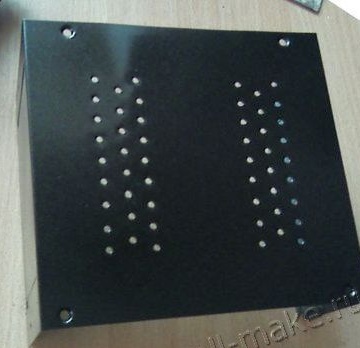
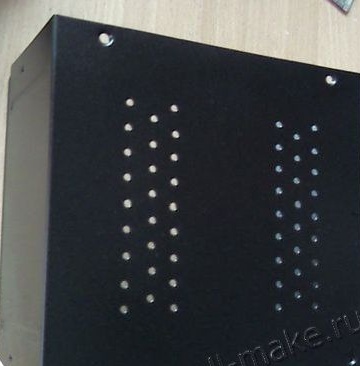
Para empezar, la unidad de fuente de alimentación se tomó de una computadora estacionaria que, después de varias modificaciones, tendría que acomodar todos los elementos de un cargador futuro. Se desmontó por completo y se eliminaron todas las piezas disponibles. Luego, el autor lo limpió de la suciedad existente y descubrió cómo colocar los elementos básicos necesarios para un futuro cargador.
Para permitir la circulación de aire dentro de la caja para enfriar los elementos calefactores del dispositivo, se decidió hacer varios agujeros en la parte superior de la caja. Primero, se realizó el marcado para esto con una regla y un marcador, ya que el autor quería lograr la apariencia del dispositivo de fábrica, por lo que todo se hizo de la mejor manera posible. Después de eso, se hicieron dos hileras de pequeños agujeros utilizando la marca con un taladro.
Dado que el dispositivo será universal, tendrá varios reguladores y una escala con un amperímetro, que se mostrarán mejor en un panel frontal del dispositivo. Por lo tanto, con la ayuda del mismo ejercicio, así como los archivos y otras herramientas que estaban a la mano del autor, se preparó el frente del caso para la futura retirada de los reguladores.
Se instalará un radiador en el panel posterior, por lo que también se ha modificado.
Paso dos: hacer un amperímetro.
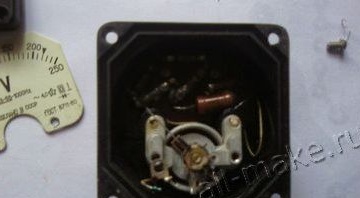
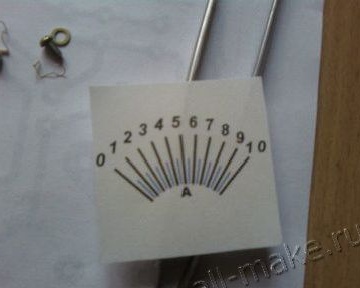
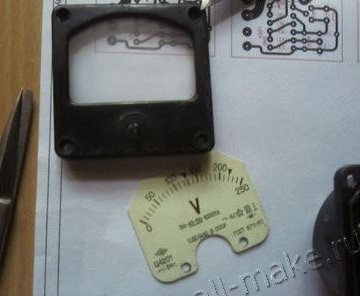
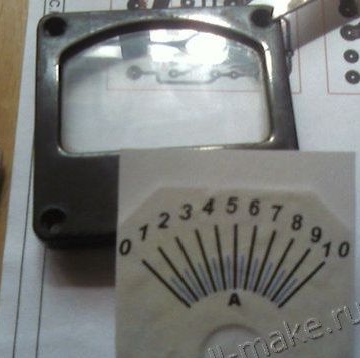
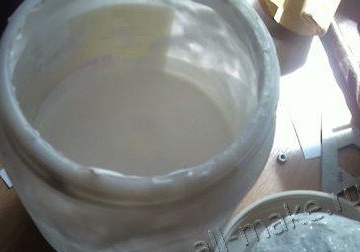
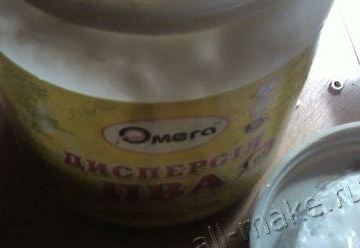

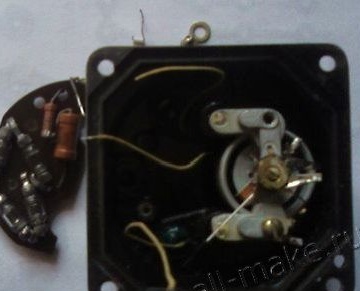
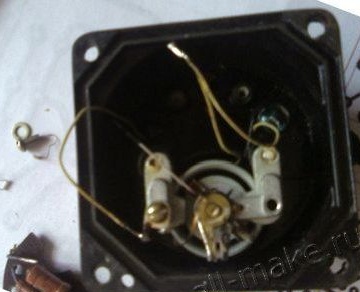
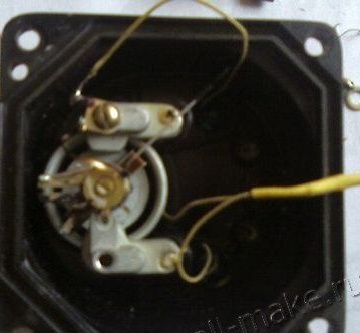
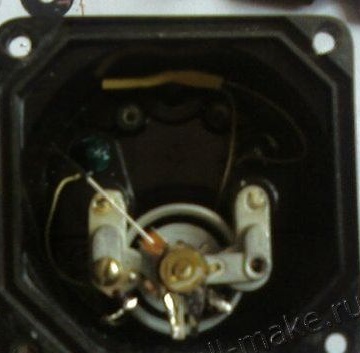
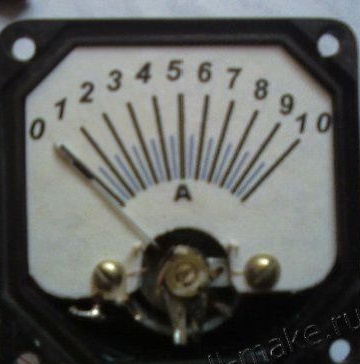
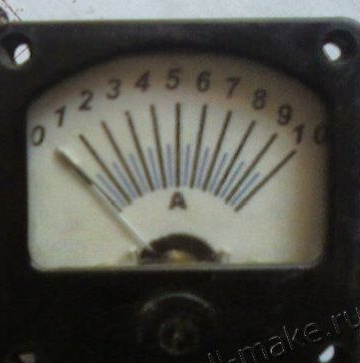
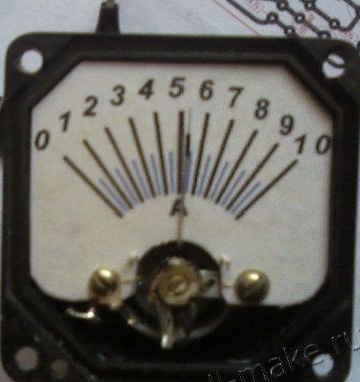
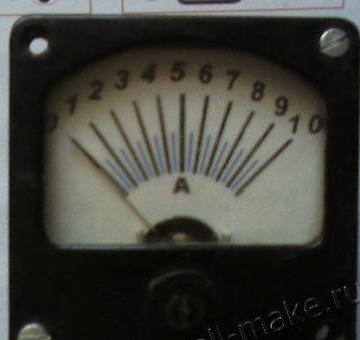
Para poder ver las lecturas del cargador, se decidió conectar un amperímetro directamente a él. Pero como no había un amperímetro adecuado entre las existencias disponibles, el autor decidió hacerlo con un viejo voltímetro de 250 V, ya que tiene una escala lineal, por lo tanto, sería un buen ajuste para este dispositivo. Durante la modificación, se eliminaron resistencias adicionales y un rectificador, y las conclusiones simplemente se soldaron a los terminales. La escala se dibujó en el programa de diseño Front, después de lo cual se imprimió con una impresora y se pegó a la antigua escala del voltímetro.
El cable PDSKT encontrado en el taller tenía 2,15 m de largo y 1,6 mm de diámetro y se utilizó como derivación para un amperímetro. Este alambre fue enrollado alrededor del marco, después de lo cual se fijó con hilos y se rellenó con resina epoxi, fijando así la estructura de manera confiable. Teniendo en cuenta que esto es suficiente y que una diferencia en las lecturas del 5% no afectará significativamente el funcionamiento del dispositivo, pasó a la siguiente etapa de creación de un cargador.
Paso tres: preparación y colocación de los elementos principales del cargador en la carcasa.
Cuando se completaron las etapas preparatorias, el autor procedió a colocar los elementos básicos dentro del dispositivo. Para comenzar, comenzó a reelaborar el transformador existente en 27 V. Fue rebobinado con un cable de cobre con un diámetro de 2.2 mm, aunque habría surgido un bus de 1.6 mm o un área de aproximadamente 4 mm cuadrados. Después de eso, ya se colocó dentro con un voltaje de 18 V en el devanado secundario y con una potencia de 120 vatios o más.
Se instaló un radiador en toda el área de la pared posterior, que consta de dos partes conectadas por pasta térmica. Se conectó a este radiador un tiristor KU202N con una capacidad de 10 A. Además, un puente de diodo de 35 A se unió al mismo radiador ensamblado.
Para construir el regulador de corriente, el autor usó un generador de pulso ensamblado a partir de transistores CT-315 y CT-361, aunque pueden usarse otros con un voltaje de 30 V y una ganancia de más de 100. Un matiz importante es que si toma transistores con una gran extensión, entonces a pequeña Las corrientes pueden interrumpirse la generación, por lo que es mejor utilizar ambos transistores con ganancia cercana, pero con conductividad diferente.
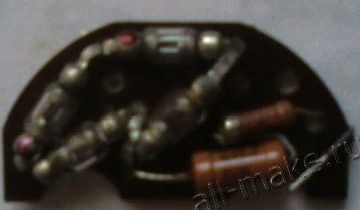
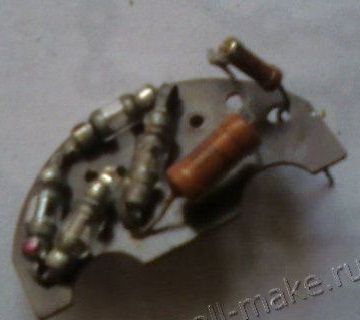
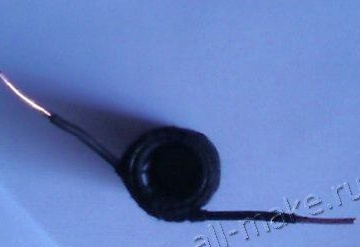
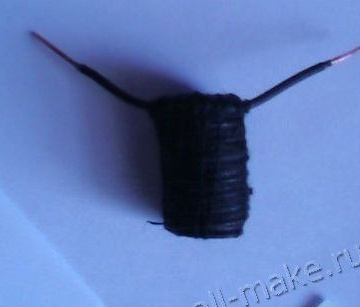
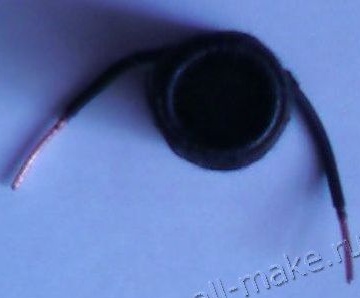
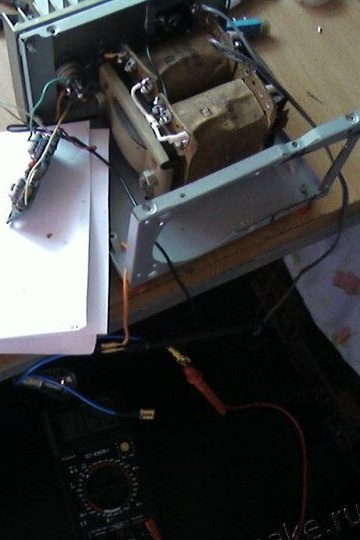
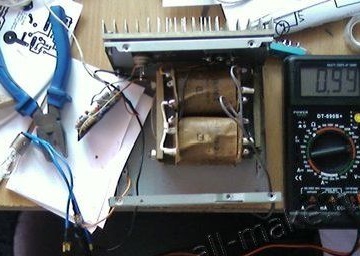
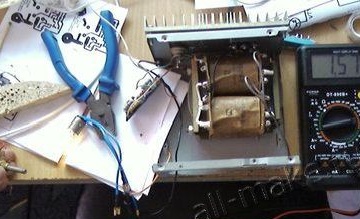
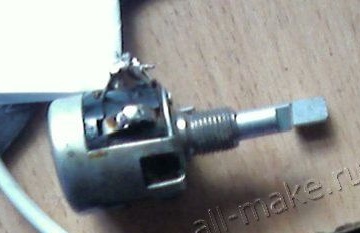
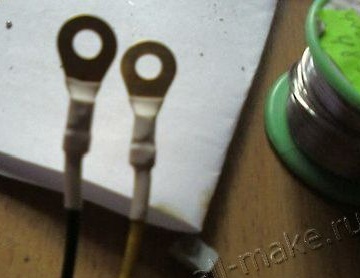
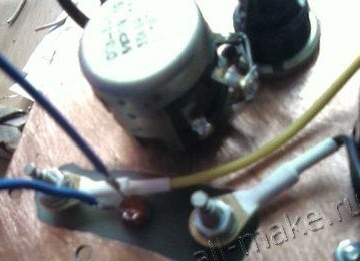
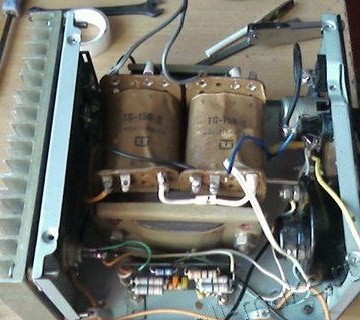
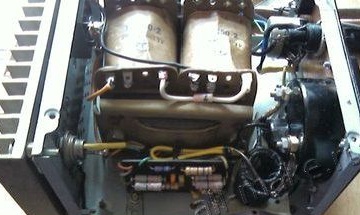
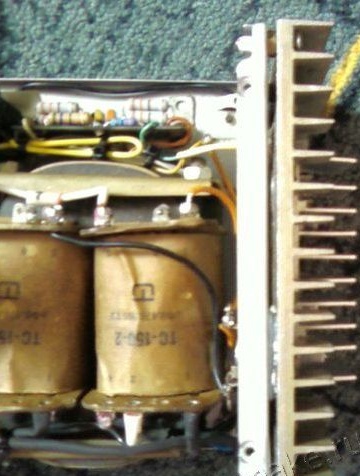
La resistencia variable dual disponible con una resistencia de 33 kOhm también se modificó para crear un regulador de cargador. Para reducir el umbral a 0.5 V, el autor hizo paralelo la resistencia y se obtuvo un valor de resistencia de 16.5 kOhm, respectivamente. Todo esto se hizo para un rango más amplio y, en consecuencia, una mayor versatilidad del cargador resultante, por lo que si solo necesitara cargar baterías de 12V del automóvil, habría surgido una resistencia variable de 4.7 kΩ, pero el autor decidió centrarse en la versatilidad del dispositivo.
Paso cuatro: crear un esquema.
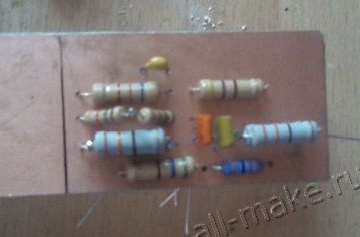
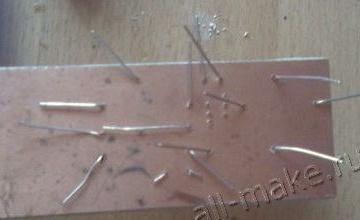
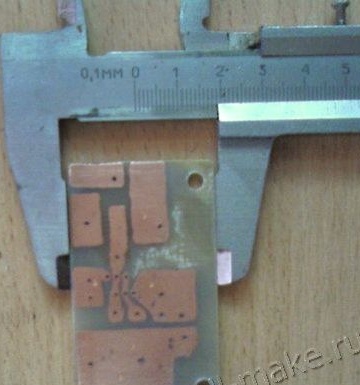
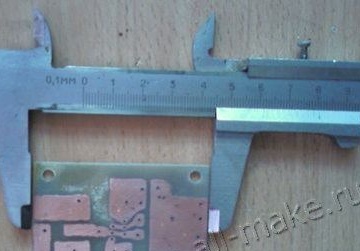
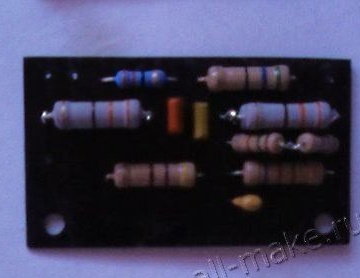
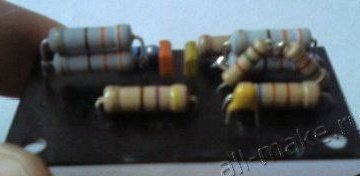
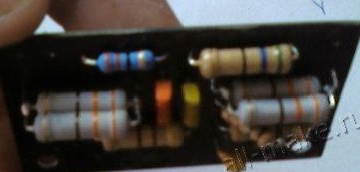
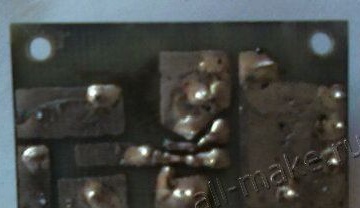
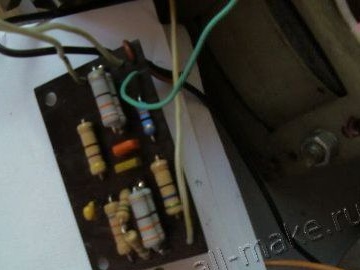
Dado que las dimensiones de la carcasa utilizada son limitadas, para crear el circuito, el autor decidió utilizar una placa de circuito impreso, aunque se puede hacer con una instalación con bisagras.
El autor también hizo la placa de circuito por sí mismo a partir de los medios disponibles. Le llevó aproximadamente media hora grabarlo, después de lo cual se lavó, y el autor procedió a soldarlo, estañarlo y, en consecuencia, instalarlo en la carcasa del dispositivo.
Quinto paso: crear un panel frontal para regular el cargador y pintar.
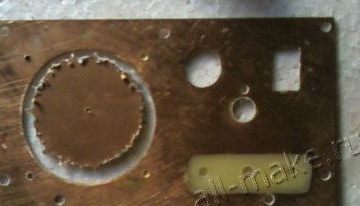
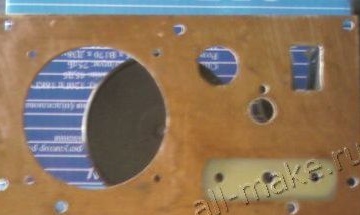
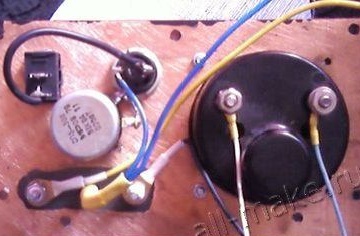
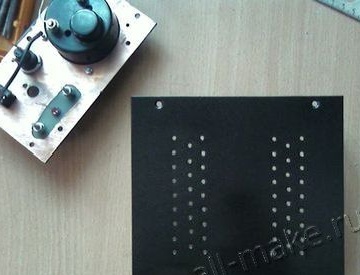
Como material del panel frontal, el autor eligió fibra de vidrio. Estaba grabado en ambos lados en las terminales. Además, de acuerdo con las marcas marcadas, se cortaron agujeros para fijar e instalar bloques de terminales, indicadores, reguladores, un interruptor, un fusible y una escala de amperímetro.
Después de eso, el panel resultante se unió al cuerpo principal con tornillos autorroscantes y todos los controles se retiraron y se fijaron en sus agujeros correspondientes.
Luego, tomando la pintura metálica negra que el autor había dejado después de pintar el parachoques de su automóvil, la usó para pintar todo el cuerpo del cargador resultante.
Puede ver el resultado en las fotografías, el dispositivo tiene un aspecto muy agradable y parece que fue ensamblado en alguna empresa, y no en el garaje.
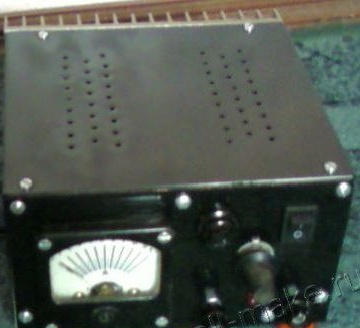
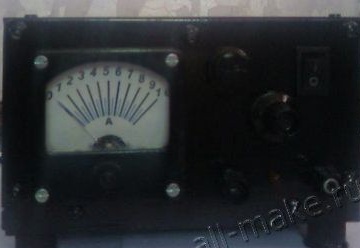
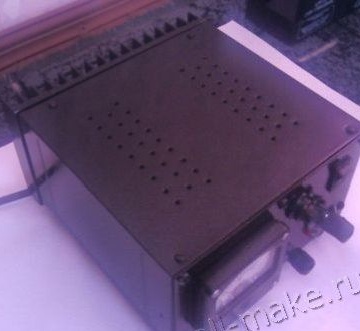
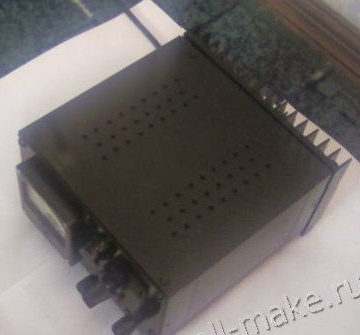
Paso seis: Indicaciones de prueba.
El dispositivo se encendió por la noche para cargar una batería 6ST90. La batería se cargó durante aproximadamente 12 horas con una corriente de carga de 8A. No se detectaron averías o fallos de funcionamiento bajo dicha carga. El calentamiento era pequeño, debido a la buena transferencia de calor y la transferencia de calor de los radiadores, el transformador no se calentó mucho. De esto se deduce que este cargador es completamente funcional y confiable.
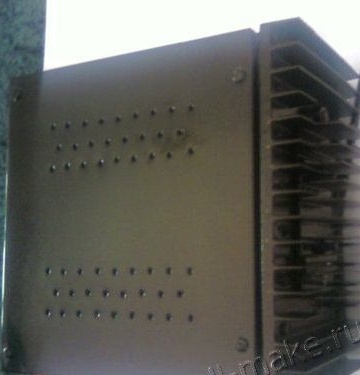
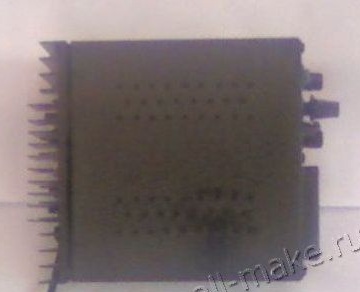
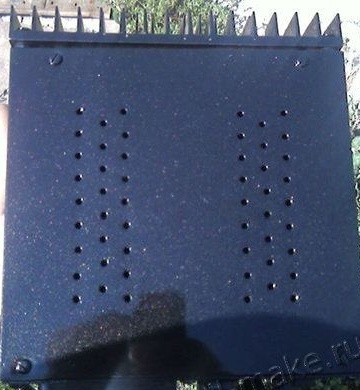
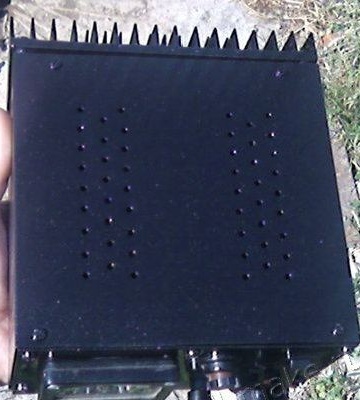
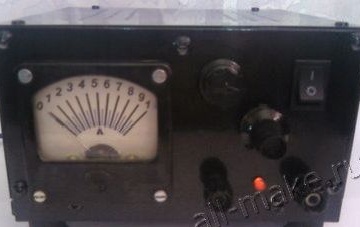
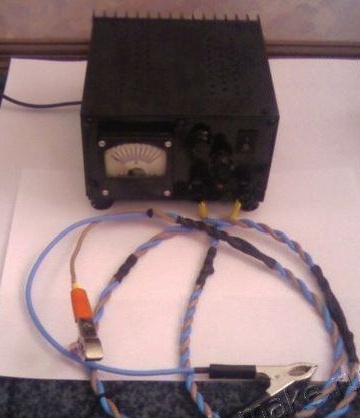
Puede encontrar información adicional en el enlace "fuente" a continuación, donde también puede hacer preguntas al autor de este dispositivo.