Quiero hablar de mi hecho en casa basado en un ventilador (refrigerador).
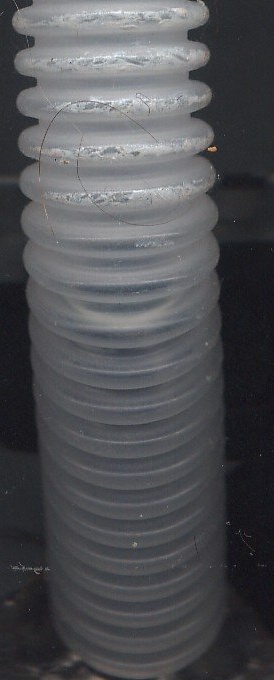
Decidí hacer una campana para soldar.
Quería que no fuera ruidoso, que fuera lo suficientemente productivo y que al mismo tiempo el tubo de salida tuviera un diámetro pequeño para no perforar agujeros enormes en las paredes.
Decidí usar el ventilador que se usa en las computadoras.
Por qué Son sin escobillas, muy poco ruidosas, bastante productivas y duraderas.
En la punta de mis dedos estaba esto:
Toma térmica
Potencia 12 V, consumo 0.13 A. Tenía poco interés.
Necesitaba saber su rendimiento.
Y entré en línea, en la marca de ventiladores TT-9025A, encontré 56 CFM.
CFM es una medida del flujo de agua en inglés antiguo. Pies cúbicos por minuto.
Pero, ahora se aplica al flujo de aire, a los ventiladores, por ejemplo.
Llegué a la conclusión de que 56 CFM son suficientes para mí para esta instalación, especialmente dado que este refrigerador funciona bien, lo sabía por el trabajo anterior con él.
Decorativo - celosía protectora para él que tenía, lo encontré. El ventilador es lo suficientemente potente, de alta velocidad, el impulsor tiene siete aspas y corta fácilmente los dedos. Como resultó más tarde, esta parrilla me ayudó a comprender cómo lograr un resultado positivo en la fabricación de esta campana.
Se necesitaba alguna base para montar los componentes de la campana.
La elección recayó en una placa rectangular para de muebles. Solía recoger mi tarea en este plato. Son visibles cuatro amortiguadores pegados del material de embalaje del puntero láser chino.
Según mi idea, se necesitaban una placa de estaño y un tubo con un diámetro de diez milímetros para poder soldarlos. Vi la cubierta de una unidad de CD-ROM desarmada y desactualizada y una espiga de marco con un hilo derribado.
Afilado de esto la parte de salida de la campana. Corte aproximadamente la cubierta de la unidad con unas tijeras para metal. Enderezado con alicates y un martillo. Marqué agujeros en la pieza de hierro para el tubo y para conectarlo al ventilador. Atornilló y taladró agujeros con taladros de los diámetros requeridos.
Limpié los bordes del orificio para el tubo y un extremo de la parte exterior de la espiga inútil del marco. Soldar el tubo a la pieza de hierro. Apliqué la llamada grasa de soldadura. Solda bien las piezas de acero. Y no se propaga, como algunos otros flujos activos. El hecho de que las piezas son de acero, primero se verifica con un imán.
Soldaba con dos soldadores al mismo tiempo, ya que es difícil calentar las glándulas. Calentó 80 vatios con un soldador, y 40 vatios, de hecho, soldaron con otro. Después de enfriar la estructura, los restos de grasa de la soldadura se lavaron con solvente 646. Verifiqué la resistencia de la conexión y si había algún espacio alrededor de la circunferencia de la soldadura.
Había ranuras en el tubo desde la espiga del marco (de acuerdo con el principio de su funcionamiento). La cubierta de la unidad también tenía ranuras y agujeros para diversos fines. Lo sacudí, lo sellé con cinta aislante.
Cuando me preguntaba cómo ensamblaría la estructura, lo primero que hice fue examinar cuidadosamente el refrigerador desde los lados. En una de ellas encontré flechas que mostraban en qué dirección gira la rueda del ventilador y hacia dónde sopla. En consecuencia, llevé el cable de alimentación a un lado y además lo aseguré con una abrazadera.
Después de eso, presentó todos los componentes en serie, de acuerdo con su idea de crear esta campana. Luego los conectó con tornillos. Los tornillos autorroscantes tuvieron que seleccionarse de diferente longitud y rosca. Los atornillé y los retorcí más de una vez.
Después de eso, usando pequeñas esquinas de metal y tornillos para madera, fijé toda la estructura a la base.
El momento más emocionante ha llegado. Probar la instalación en acción.
De acuerdo con la polaridad de los cables del enfriador (como de costumbre, más - rojo), conecté la fuente de alimentación de mi laboratorio después de ajustar el voltaje a 12 V.
El ventilador comenzó a girar. En primer lugar, traje una hoja de papel A4 a la red decorativa protectora. Se sintió atraído por la rejilla. Entonces, todo está ensamblado correctamente.
Después de eso, llevé la hoja al tubo de salida. La hoja se rechazó. Eso es correcto también. Pero, se desvió muy débilmente. No necesito esa capucha.
Entonces comencé a conjurar con agujeros y grietas. Esto es:
Ranuras en las juntas de los componentes de la instalación, agujeros en la rejilla decorativa protectora. Pegué todo de manera confiable, excepto la parrilla, con cinta aislante de alta calidad.
Extraño, pero la capucha comenzó a funcionar peor. Entonces comencé a pelar, a veces cortaba la cinta aislante.
Los resultados cambiaron al azar.
Empecé a detenerme.
¡Y, de repente, recordé la ley de Bernuli!
Lo que dice que en líquidos y gases, al aumentar la velocidad del flujo, su presión disminuye. Y viceversa.
Me di cuenta de que necesito hacer un ajuste suave de alguna manera, y al pegar y despegar la cinta eléctrica no lograré nada.
En el centro de la rejilla decorativa y protectora, perforé un orificio que es comparable en diámetro con el diámetro interno del tubo de salida.
E hizo una válvula de compuerta o compuerta ajustable especial, y puedes llamarlo así.
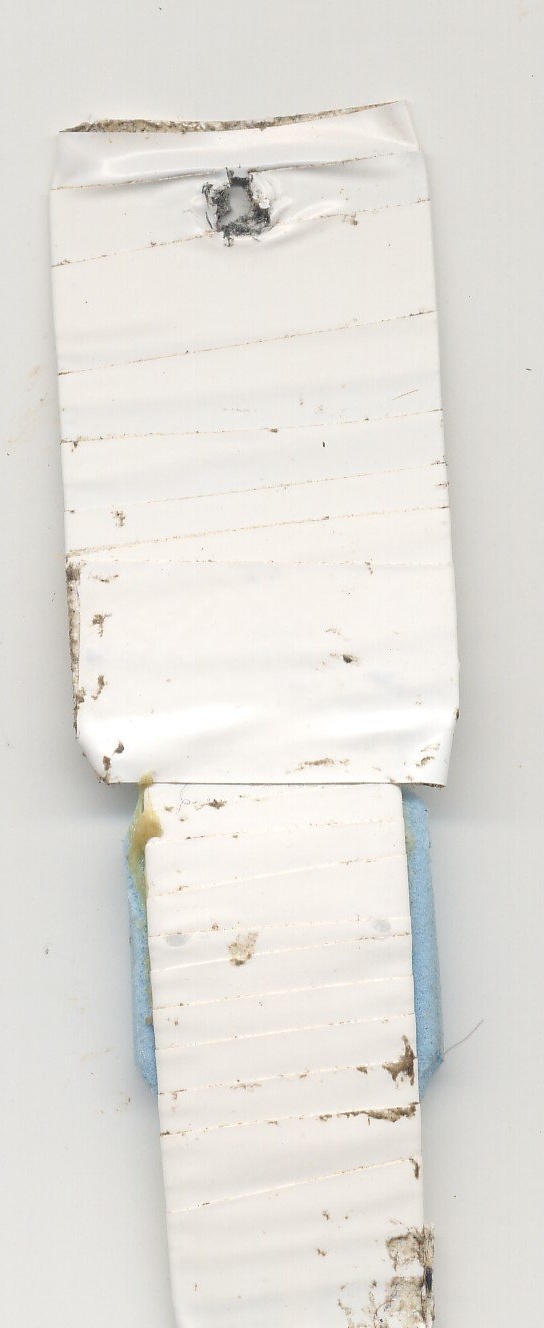
Tomé una placa bastante elástica de alguna aleación, de una técnica desmontada.
Corté la forma deseada con unas tijeras para metal. En un extremo de la placa, hice un agujero para el montaje. Envolví el plato con cinta aislante y pegué una almohadilla de material elástico que me llamó la atención.
Durante mucho tiempo doblé la placa en todos los sentidos, tratando de asegurarme de que el amortiguador se superpusiera a un agujero grande en el centro de la rejilla decorativa protectora en el grado necesario. Al mismo tiempo, el amortiguador no debe cambiar espontáneamente su posición. Para esto, necesitamos una placa elástica y una almohadilla.
Como resultado, resultó. El amortiguador permitió regular con mucha precisión la relación de flujos de aire entrantes y salientes.
Además, ¡logré lo increíble! Haga el ventilador diseñado estrictamente para soplar, sin cambiar la dirección de rotación del impulsor, sin moverlo en la carcasa, ¡trabaje con succión!
¡Las cuchillas giraron en la misma dirección, y el refrigerador aspiró aire!
Decidí asegurarme de que esto no sea un sueño.
Puso la punta del dedo en el tubo de salida y lo envolvió firmemente con cinta aislante. En una posición del amortiguador, la yema del dedo se infló, es decir, se creó una sobrepresión en él, y en la otra posición del amortiguador se contrajo, en él se creó un vacío. Cuando se apagó el ventilador, la yema del dedo tomó su forma habitual (la presión en él se igualó con la presión atmosférica). En cierta posición de la válvula, con el ventilador en funcionamiento, no hubo movimiento de aire, lo que no contradice las leyes de la ciencia.
Tengo un video de esta prueba. Adjunto capturas de pantalla de este video con mis explicaciones:
Vista posterior de la instalación.
Se coloca la punta del dedo en el tubo de salida.
Alta presión dentro de la punta del dedo.
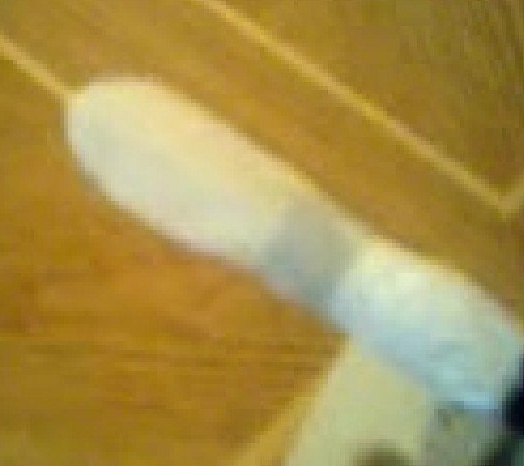
Dentro de la yema del dedo
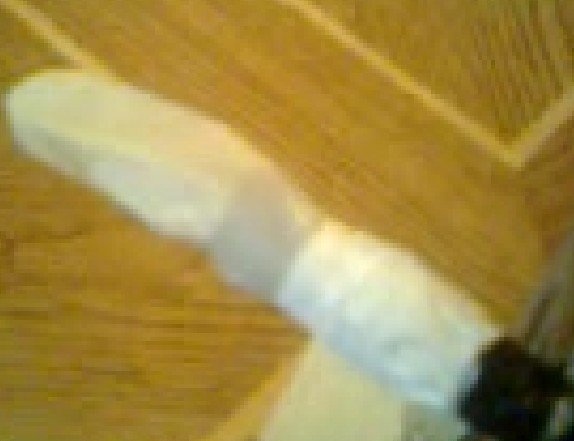
Proceso de ajuste de aletas
Con un cambio brusco en la posición de la válvula, debido a cambios en la velocidad y la presión del flujo de aire, hubo un sonido peculiar a corto plazo, similar al golpeteo. Cuando trabajaba en modo normal para campana o succión, el ventilador era casi inaudible, incluso cuando estaba cerca.
Ahora mostraré un diagrama de instalación simplificado.
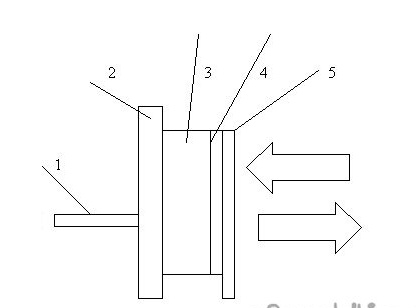
1 - tubo de salida, se conecta una manguera flexible de pequeño diámetro, que se muestra fuera de las instalaciones.
2 - placa
3 - ventilador (enfriador)
4 - decorativa - celosía protectora
5 - obturador ajustable
Las flechas indican que el aire puede moverse en ambas direcciones o no moverse (dependiendo de la posición del amortiguador).
Después de un tiempo, decidí mejorar este sistema. Sus dimensiones disminuirán, y el nivel de ruido no cambiará, la potencia aumentará. Sé cómo lograr esto.
Espero que haya estado interesado en familiarizarse con mi producto casero y, basándose en lo anterior, hacer algo así.
Sinceramente, autor.