¡Saludos a los maestros!
Después del tormento, digamos, decidí hacer un kit de carrocería para la máquina de soldar. El tormento era que, trabajando en alturas, no siempre era conveniente tomar los electrodos con la mano en la capucha e intentar ponerlos en el bolsillo o en el bolso de la cintura, dormían constantemente, etc., y el martillo se perdía constantemente incluso si trabajaba en el taller. Y también en el taller tuve que buscar paquetes de electrodos, luego se cayeron en algún lugar, luego puse material encima, etc.
Se me ocurrió la idea de unir todo al cuerpo del soldador ...
Si bien el trabajo en la calle no era posible debido a las condiciones climáticas, pero no podía permanecer inactivo, se ocupó hecho en casa.
Herramientas y materiales:
- Amoladora angular (amoladora)
- ruedas de corte para metal
- tuberías de alcantarillado F40mm (2 piezas)
- tapones para tuberías de alcantarillado Ф50мм (2 piezas)
- tapones para tuberías de alcantarillado F110mm (4 piezas)
- remaches de escape 3.2x10; 3,2x6; 4x10
- remachador
- brocas para metal de 3,5 mm; 4 mm; 16mm
- destornillador o taladro
- pieza de tabique de paneles de yeso de perfil 50x50
- línea de ropa
- soldador
- estación de soldadura
- cinta métrica o regla
- lápiz, marcador, punzón (se usaba para dibujar el contorno, era más conveniente)
- Arandelas galvanizadas de 4 mm
- un martillo
- tornillo de banco o yunque
Paso 1: Material y colocación en el caso.
Antes de emprender y hacer lo que se pretende, es necesario tener en cuenta las dimensiones del cuerpo del aparato, las dimensiones que necesita saber para lo siguiente:
- las dimensiones deben ser compactas
- la colocación debe estar en un lado
- durante la operación, el uso del kit de cuerpo no debería crear molestias
Para el tubo debajo de los electrodos, lo más óptimo es una tubería, una alcantarilla de 40 mm es bastante adecuada para esto. Tiene sus ventajas: el plástico es lo suficientemente fuerte, barato y, lo más importante, ligero.
Teniendo troncos de tubería de 50 mm de longitud suficiente en la granja (solo para determinar la ubicación), para comprender cómo se ubicará el tubo, los usé para determinar el lugar en el cuerpo. Para medir las dimensiones con una cinta métrica, lo consideré innecesario, porque para determinar, de hecho, es más conveniente cuando ya sabes lo que vas a hacer.
Mientras dominaba el trabajo con soldadura, estaba convencido de que los electrodos cortados por la mitad son más convenientes que en toda la forma.Ahora los corto constantemente en dos partes de 17.5 cm y en las partes cortadas derribo el polvo con un martillo (no recuerdo cómo se llama correctamente). Un tubo de 35 cm de largo para todo el electrodo no se podría colocar de manera compacta en una carcasa de estaño, de modo que otras ideas también se colocarían una al lado de la otra.
Paso 2: tubo para electrodos.
Habiendo descompuesto los electrodos inicialmente en las tuberías 50 y 40, me di cuenta de que la tubería 40 es más amplia, es decir hacer un tubo con dos tubos de 40 fue más adecuado en tamaño que con un 50. Pero los tubos se necesitaban con una campana para la conexión (explicaré por qué), y como tenía troncos sin enchufes, tuve que ir a comprar. También tuve que comprar dos tapones para la tubería número 50, de los cuales haré una tapa para que los electrodos no se derramen si la soldadura está inclinada.
Compré tubos de 25 cm de longitud, encontré 15 cm, pero por alguna razón no estaban a la venta. Cortaré no 17.5 cm del borde, sino un poco menos de 17.5, a partir del cálculo de que la cubierta también tiene una profundidad de casi 2 cm. Puse las cubiertas futuras en las tomas de tubo de 40 mm y formo la cubierta.
Corté menos para que después de cortar el exceso en la tubería, los electrodos sobresalieran sobre los bordes al final del trabajo en el tubo. Es mejor tomar el electrodo inmediatamente que tratar de encontrarlo con los dedos adentro.
La longitud es de 17.5 cm, y mide 18 cm (margen de 0.5 cm) desde la costilla en el tapón mismo, y desde allí hizo una marca en los propios tubos.
Trompeé los tubos a lo largo de la marca con una hoja de papel. Lo envolví alrededor del tubo, conecté los bordes del papel y pegué estos bordes con cinta adhesiva, lo corté con las orejas, tiene un regulador de velocidad y no tuve que cortar el plástico con un cuchillo de oficina.
Como los tubos estaban orientados, decidí devolver los chaflanes, serán necesarios para que en el futuro sea posible soldar la parte inferior.
El plástico para el fondo del tubo se cortó de los mismos tapones solo para la tubería 110.
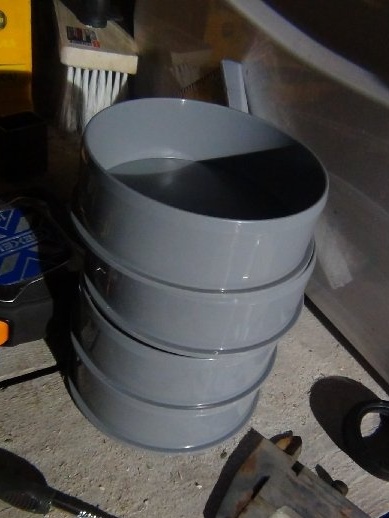
En algún lugar tenía piezas del mismo plástico, pero era demasiado flojo para buscarlas, así que decidí comprar estos tapones. Para obtener un plástico plano para la parte inferior de ellos, corté un anillo de estas cubiertas.
Todavía se necesitarán los anillos restantes, los uso como barras de soldadura, ya que los corté previamente a un ancho de 3-4 mm con unas tijeras de metal.
No queriendo pasar tiempo marcando con un marcador, coloque los tubos de corte en plástico y arañe la circunferencia de los contornos con un punzón. Luego cortar con tijeras para metal. Como resultado, dos fondos, queda por soldarlos.
Cuando se usa una estación de soldadura, es decir soldar con una barra, tachuelas hechas con un soldador ordinario a lo largo de la parte inferior y el tubo, estos puntos mantendrán la parte inferior en su lugar y no permitirán que las alas se muevan cuando se suelden con una barra de plástico.
Resultó muy personal, alise los bordes ásperos con un soldador común. Casi vendible.
Casi todo, pero queda por pequeño: la portada
Las protuberancias en las tapas no le permitirán colocar los tubos según lo planeado. Tendremos que cortarlos por un lado y también cortar el chaflán. Este trabajo facilitará su soldadura en el futuro.
La decisión de cortar así está determinada por el hecho de que es mejor cortar las costillas y los tubos más cerca uno del otro que dejar todo como está y atrapar el milímetro entre los tubos. Pero las dimensiones del tubo están limitadas por las dimensiones de la pared de la carcasa de estaño de la soldadura.
Entre ellos fueron soldados por piezas que quedaron después de cortar los fondos. Recortar ya no es adecuado, pero solo para tal trabajo.
Para que la tapa no se rompa en el lugar de soldadura donde estaban las costillas, decidí soldarla también a los lados. Cuanto más fuerte sea la tapa, más durará, y una idea adicional requiere que esté tan soldada de lo contrario se romperá.
La producción de estas tuberías se realiza por moldeo, si no me equivoco con el nombre del proceso.
Las extensiones de tubería, dentro de ellas son sellos de goma en el interior, tienen una forma desigual. Tendrá que estar molido, de lo contrario, la cubierta fabricada no se usará en la campana y tendrá que volver a hacer una cosa.
Después de este trabajo, procedemos a la fusión de dos tuberías en un tubo.
Antes de soldar los tubos, es necesario ponerles la tapa y fijarlos con cinta adhesiva, esto no permitirá que los tubos se muevan uno con respecto al otro durante el proceso de soldadura.
Mientras se trabaja con plástico, quedan muchos restos, pero para no tirar el material, de hecho, lo pusimos en funcionamiento, cortamos estos restos en pedazos y los pusimos en contacto con los enchufes, y dado que no tenía sentido soldar la estación (solo 1-1 , 5 cm) soldados con un soldador. Al final hizo lo mismo.
Tenía que pensar en la bisagra de la tapa, había hechos que no deberían abrirse en una dirección, de lo contrario no sería conveniente para ella usar (quedará claro por qué). Para unirlo a un resorte, un trozo de tela o un eslabón giratorio no sería estéticamente agradable, así que decidí usar un trozo de cordón de polipropileno. En este cable, la tapa puede abrirse y deslizarse en cualquier dirección, esta idea resultó, por cierto, la tapa puede abrirse y rellenarse para el contenedor con los restos de los electrodos, llamé a este contenedor un "cenicero" (el nombre más lógico), y estará ubicado justo debajo del tubo .
Hasta que quité la cinta, marqué los lugares de perforación para remaches de 3.2x6 mm.
Después de afeitarse con un cuchillo, los extremos peludos del cordón se trataron con un soldador. Luego, para instalar el remache, lo atravesó con un punzón y tiró de él. Antes de instalar los remaches en plástico, es mejor colocar la arandela en la parte posterior, vale la pena hacerlo, porque los remaches son remaches y durante la instalación pueden romper el plástico.
La tapa no será una tapa si se cuelga.
Era necesario encontrar una cerradura, pero simple, sin llave. Por conveniencia, es mejor hacer posible abrir con un dedo.
Hizo un simple pestillo de bloqueo de la placa.
La placa se cortó unos 6 cm, se hizo a esta longitud específicamente para que hubiera un lugar para abrir un dedo y se apoyara contra el borde (ver foto).
Para evitar que se rompa durante las primeras pruebas, fue soldado tanto a lo largo del borde como a los lados, después de tal soldadura comenzó a funcionar como un resorte.
En lugar de un bucle, esto no es una cerradura, hizo una pequeña repisa similar a una aleta de tiburón. Para hacerlo, debe perforar la placa en la tubería, establecer la dirección. Si esta "aleta" se suelda a la superficie, entonces se romperá, y si se inserta en el agujero y se derrite desde el interior, será mejor sostenerla, lo hice.
La placa para la aleta se cortó 1 cm de largo.
De todos modos, desapareció del exterior.
Ahora le damos forma a la "aleta", la soldamos con un soldador y alisamos el borde derretido. Bisel hecho hacia la tapa, ahora todo funciona como un pestillo. Pero a los lados de esta boquilla tuve que modificar el archivo para que la placa se colocara sin problemas.
Paso 3: colocar el tubo.
Antes de perforar, es necesario quitar la carcasa para que las virutas no entren en los circuitos y contactos.
En un caso extremo, puede desenroscar la pared y colocarla debajo de cartón o papel grueso, como hice yo.
Pasé por muchas monturas en mi cabeza, pero decidí detenerme en lo que describiré más adelante.
No se requirió una fijación muy grande para no interferir si se retiraba el tubo, porque No siempre trabajo en altura y no es necesario mantener constantemente el tubo en el cuerpo del dispositivo.
Como resultado, la decisión adicional resultó ser el tema, es decir, más adecuado
El principio de fijación como válvula o perno.
Corté todos los elementos de los 110 enchufes.
El soporte está diseñado como un bolsillo. Para hacer esto, debe cortar dos partes idénticas para un montaje, en una de ellas se cortará un cuarto donde se insertará el perno de barra. El que se cortará la parte será adyacente al cuerpo. Dichas partes necesitarán 4 piezas.
Para que el cerrojo encaje en el pestillo sin problemas, se debe hacer un espacio de 1 mm entre las partes. Al cortar el anillo del enchufe 110, hubo protuberancias, fueron útiles.
Conecté las dos partes del soporte y simplemente solde a lo largo del borde con un soldador común. Como resultado, tenemos un soporte para la parte inferior del tubo. Hizo todas las partes de manera similar (foto abajo).
El borde recortado se obtiene en un ángulo de 90 grados, se apoyará contra las monturas mismas, donde el mismo corte. Para evitar esto, la amoladora corta el chaflán (ángulo arbitrario).
Como resultado, esta decisión facilitará la extracción y reinstalación del tubo.
Zasov hecho de placas del trozo 110. Estas barras de perno se soldarán a los tubos del tubo. Debido a tales bloqueos, el tubo se sujetará firmemente a la carcasa de soldadura.
Corté los chaflanes con la amoladora, así como con las monturas, en el proceso probé esta cerradura y me aseguré de que los chaflanes deberían estar tanto en el soporte como en los pernos.
Como todos los chaflanes están hechos, debe soldar las molduras a los tubos y puede comenzar a perforar agujeros para los remaches en el propio cuerpo.
¡Pero no tan simple! Antes de perforar, asegúrese de que los remaches instalados no interfieran con la instalación de la carcasa en el lugar del cuerpo principal donde se encuentra el interior del dispositivo. La carcasa se fija con tornillos ordinarios a un marco de metal. Falta este momento no sin importancia, tendrá que perforar agujeros.
Midió 5 mm desde los agujeros de montaje en el centro del avión y dibujó una línea que delimita el borde de los remaches con un lápiz.
Como todos están marcados, puedes terminar los cerrojos.
Preliminarmente, después de colocar los sujetadores y los adornos con el tubo en la carcasa, comenzó a moverse de lado a lado todos los detalles para determinar la ubicación. Tan pronto como decidí la situación en los tubos, noté los lugares donde se soldarían las tiras. El tubo se obtiene en un ángulo relativo al fondo de toda la soldadura.
Soldé los pernos con una estación de soldadura a lo largo del zócalo y en la parte inferior cerca del fondo con una varilla y restos de esos restos del enchufe.
Antes de perforar, cuando el lugar ya se ha determinado con precisión, sin marcar con un marcador, lo hizo más fácil, lo presionó firmemente con la mano contra el cuerpo y perforó tanto los sujetadores como la carcasa con un destornillador. Establecer remaches de 4x10 mm de grosor y longitud lo más óptimo.
Después de completar este trabajo, lo probé levantando solo el tubo, nada roto, todo se mantiene apretado. No puede tener miedo de que algo se caiga en el proceso.
Paso 4: Capacitancia para residuos de electrodos.
Decidí hacer un contenedor para los restos de los electrodos debido a los pequeños restos que quedan.
Trabajó en altura, cocinó arcos en un cobertizo temporal de metal y arrojó el resto bajo sus pies. Bajando la escalera para el siguiente lote de electrodos, pisó un bulto así, atravesó la suela de mis boinas de trabajo y me lastimó levemente la pierna, no mucho, pero la sensación no fue agradable.
Llamó a esta capacidad un "cenicero", porque las mismas pequeñas "colillas" de los electrodos permanecen como de los cigarrillos, lo que significa que no puedes imaginar un nombre mejor.
La granja tiene muchos restos de perfiles de paneles de yeso, entregué chatarra y a la vista había una pieza del perfil de partición de 50 mm por 50 mm. De eso decidí hacer.
Las dimensiones salieron 7x5x5 cm, donde 7 cm es la altura.
La pieza en sí era de unos 50 cm de largo, y solo necesitaba 17 cm.
La caja era la más simple. Corté el exceso y me doblé por las ranuras de la caja, como en origami.
Cómo arreglarlo en el soldador, de hecho, ¡ya sabes la respuesta! Igual que para el tubo. Necesito que estos cierres tampoco se noten si el cenicero se retira como innecesario.
Partes del perfil se doblaron con un martillo en el yunque en un plano con la parte posterior de la parte posterior de la caja, con dos orejas formadas, como un perno de barra de tubo.
La caja misma estaba montada en remaches 3.2 por 6 mm.
Como escribí anteriormente, esta caja estará debajo del tubo, pero el tornillo de la caja impidió la instalación de sujetadores, por lo que tuve que cortar las orejas para que se apoyen en el tornillo, los restos de los electrodos no pesan 10 kg, por lo que esas orejas serán normales, como dicen.
Aquí decidí hacer la parte inferior no con plástico, sino con dos arandelas debajo de una remachada.
Taladró tanto como el tubo, presionándolo con fuerza con la mano. Montajes instalados en remaches 3.2x10 mm.
Paso 5: accesorio para el martillo.
Como escribió al principio, el martillo (ciertamente apareció más tarde) y todo tipo de objetos que usaba para golpear la escoria se perdían constantemente y los lugares donde se perdieron se olvidaron ...
También decidí hacer una montura para el martillo, ya que lo hice, y demostró ser bastante funcional en los negocios.
Hacer un sujetador como en la descripción anterior no tenía sentido. Aquí comencé a descifrar cómo y dónde determinarlo ...
Muchas ideas destellaron como un viento en mi cabeza y decidieron hacer una montura inusual.
Un anillo sin usar de un trozo grande entró en funcionamiento.
En la primera foto ya podías ver este rendimiento de la montura.
Descripción adicional
Girando el borde en las manos y el martillo decidió este formulario (ver foto).
Dado que el martillo no entrará directamente a lo largo del centro, sino como a lo largo de una tangente desplazada, es necesario perforar agujeros ovalados.
Después de determinar la altura del arco en relación con el sitio de la futura fijación, hice marcas donde perforaré con un taladro de metal de 4 mm y luego con un taladro de 16 mm, el diámetro del mango del martillo está hecho de 16 varillas.
Para obtener un orificio ovalado, primero debe perforar perpendicularmente al círculo, me confundo cómo describirlo correctamente y luego girar hacia el lado de otro orificio, como resultado, la longitud del taladro permitió hacer un orificio pasante, en la dirección de la entrada del martillo y el plano de la placa, obtenemos un orificio ovalado (ver foto). Posteriormente, este soporte demostró ser el mejor y no tuvo que tener un retenedor de martillo adicional para que no se caiga.
La placa de montaje para la última fijación se cortó de los restos del trozo; también se ajustaba al ancho y al largo también.
Queda por soldar el arco al plástico, luego casi agoto los restos de plástico innecesarios. No tenía sentido en una estación de soldadura, lo convertía en un soldador ordinario.
Determiné el lugar para esta fijación en la soldadura desde arriba, hice un cambio hacia adelante para que la correa que está en el hombro en una posición tensa no interfiera con la extracción del martillo.
Remachado en remaches 3.2 por 10 mm.
El proceso de perforación, así como en casos anteriores, fuertemente presionado y perforado.
Del mismo martillo, aquí ya inteligente, resultó no ser un mal gancho para llevar un casco (ver foto).
Cuando te diriges al lugar de trabajo, tus manos están libres de material u otra cosa ...
Si tiene preguntas, contácteme, le responderé :)