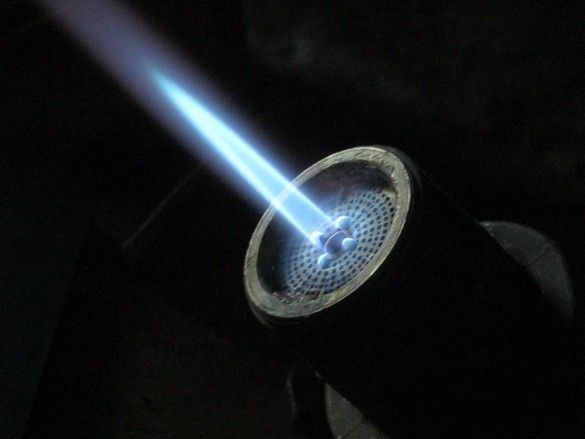
Un quemador de mesa es la principal herramienta de soplado de vidrio, sin importar si se trata de la fabricación de instrumentos de vidrio o la fabricación de figuras y decoraciones divertidas. El quemador forma una llama, conveniente para ablandar el vidrio y las operaciones posteriores con él. En este caso, se hace necesario obtener varias temperaturas y formas de la antorcha.
Por casualidad, obtuve una pequeña antorcha de vidrio que sopla sobre la mesa, formando una aguja de llama no regulada bastante delgada. Incluso cuando se trabaja con vapores de gasolina (la temperatura de la llama es más alta que la de una llama de gas-aire), la potencia del quemador no era suficiente para trabajar con piezas de trabajo tan grandes. Para algún aumento en el flujo de calor, se compilaron dos quemadores: se agregó un portátil de gas, en la dirección opuesta, o así.
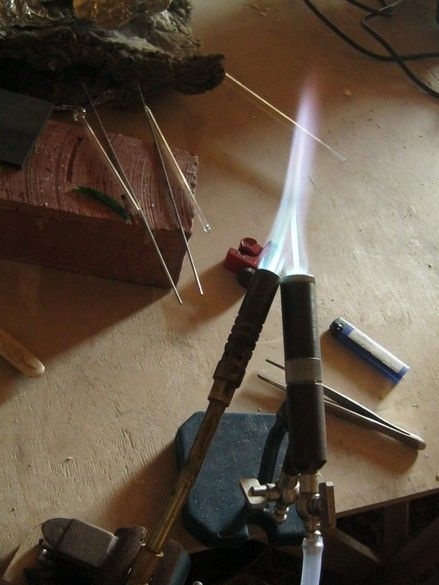
Resultó una llama esponjosa, con una aguja de alta temperatura en el centro. Las cosas se volvieron más divertidas, se hizo posible inflar un tubo de 10 mm. El siguiente paso lógico fue la fabricación de un quemador más potente que quemara vapor de gasolina.
Será un prototipo del quemador hecho de materiales improvisados, principalmente componentes de plomería. Las piezas fueron mecanizadas sin un torno de metal. El quemador funciona con vapores de gasolina y se basa en el soplador de vidrio Yuri Nikolayevich Bondarenko [1], un astrónomo soplador de vidrio que fabrica dispositivos de descarga de gas. Las soluciones de algunas unidades se tomaron prestadas de su diseño; de lo contrario, el quemador repetirá el diseño conocido por joyeros y dentistas.
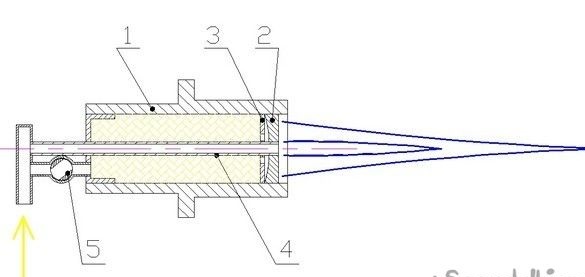
Su base es un cuerpo cilíndrico hueco 1, coaxialmente con el que pasa la boquilla 4. La llave de corcho 5 le permite ajustar la forma de la antorcha: cuando la abre, parte de la mezcla combustible ingresa al cuerpo además de la boquilla y se forma en la antorcha por la rejilla 2. Abertura 3, junto con la forma de la rejilla 2 y la cavidad lenticular resultante, concentra el flujo de la mezcla combustible principalmente a lo largo del eje del quemador. Estas partes están tomadas del quemador del mentor [1]. En el tubo de la boquilla hay varios orificios que suministran un poco de gas a la rejilla (no se muestra en el dibujo) y con el grifo 5 completamente cerrado, para formar una pequeña antorcha de soporte.No permite que la antorcha principal se rompa: la "aguja" a altos caudales de gas. Estos agujeros se seleccionan al configurar el quemador.
Herramientas, equipamiento.
Una soldadura de gas suave necesita un pequeño quemador de gas. Conjunto de herramientas de banco. Afilador electrico. Se utilizaron un torno de madera y una perforadora. Vise
Materiales
Además de las piezas de hierro, se necesitaba un tubo de cobre de 6 mm de diámetro. Soldadura de estaño y cobre No. 3, fundente. Grifo de corcho de un samovar.
La pieza en bruto para el cuerpo del quemador era un accesorio de bronce de fábrica de un taller de plomería con un diámetro interno de 30 mm. También se compraron varias partes diferentes, algunas de las cuales también se usaron más tarde como espacios en blanco para los elementos del quemador.

Uno de los accesorios se utiliza como carcasa sin cambios. El accesorio no estaba girado hacia afuera: el gran grosor de la pared y las mareas proporcionan al cuerpo una disipación de calor adicional.
Se eligió el tamaño de los tapones de plomería para que con un giro mínimo de la rosca, la parte resultante encajara en el canal interno del accesorio. Amolado madera en un torno, para esto hice un simple broche en el que planté una pieza de trabajo.
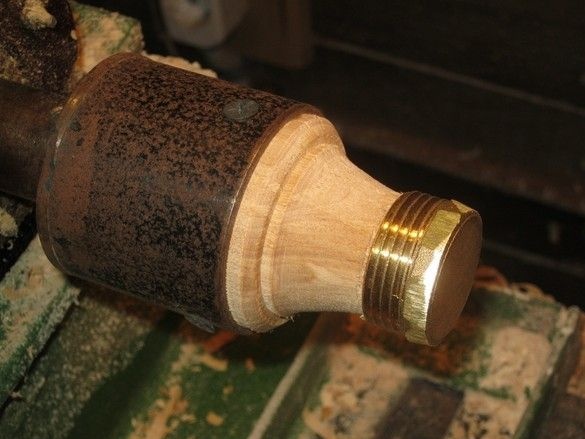
La densidad de aterrizaje permitió más, no hay forma de arreglar la pieza. Entrando fuertemente en las esquinas de un hexágono llave en mano, previamente se muelen en un molinillo. Volcaduras - alrededor de 1000 rpm, primer giro brusco con un pequeño "molinillo" - la pieza gira, el molinillo funciona. Después de terminar el archivo y la piel del medio clavada en un bloque de madera. La fijación final de la pieza de trabajo permitió probarlo convenientemente y, a menudo, en el "lugar de trabajo": la parte resultante ingresa a la carcasa con fuerza con poco esfuerzo.
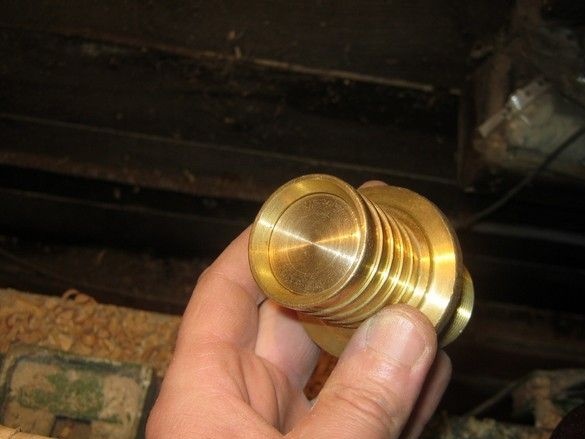
Procedemos al detalle complejo y crucial: la cuadrícula. Primero, algunas consideraciones teóricas.
La rejilla, además de distribuir la mezcla de gas combustible, también es responsable de la seguridad: no permitirá que la llama penetre en el interior y evitará un "retroceso". Esto es cierto ya que nuestra mezcla de combustible se prepara en globo "bombilla" y no como de costumbre, en el lugar del quemador. En este tipo de quemador para trabajos completos con vidrio, incluido el vidrio refractario, como Pyrex, es necesario agregar gas explosivo del electrolizador.
La llama, que pasa dentro, a través de la rejilla, se enfría tanto que se apaga. Hay un concepto: el último agujero. Este es el diámetro máximo de los orificios "profundos" capaces de realizar una función de supresión de llama, y es diferente para diferentes gases. Por ejemplo, para los vapores de gasolina en el aire, cuya velocidad de propagación de la llama es pequeña, el orificio limitante es de ~ 0.9 ... 1 mm, pero tan pronto como el oxígeno o el gas explosivo penetren en el sistema, lo que aumenta significativamente la velocidad de propagación de la llama, los orificios en la "malla" protectora tendrán que hacerse sustancialmente menos El diámetro máximo de los agujeros, por ejemplo, para gas explosivo limpio, ~ 0.3 mm, lo que representa cierta dificultad en la fabricación y operación.
Como una especie de compromiso, Yuri Nikolayevich propone utilizar agujeros en la rejilla de 0,8 mm, mientras que la medida de seguridad necesaria en el taller será un diseño bastante robusto de la "bombilla" y la "descarga" del electrolizador [1], para que puedan sobrevivir a una posible explosión sin daños. El carburador de gasolina está hecho de un cilindro de propano, lavando el electrolizador de los extintores de dióxido de carbono. Durante el funcionamiento normal del equipo, no se producen avances. En caso de violaciones de las condiciones normales de funcionamiento, se produce un aplauso que no conduce a un accidente.
La "longitud" de los agujeros de malla, da su grosor. Dada la forma lenticular, el grosor de la malla debe ser de 3 ... 4 mm en la parte delgada y de 6 ... 7 mm en los bordes. No había una placa terminada de tal grosor; tuve que buscar un donante. Resultó ser un grifo anticuado bastante masivo para el baño. Se cortó una pieza relativamente uniforme de la pared, de la cual fue posible cortar un espacio en blanco para la cuadrícula.
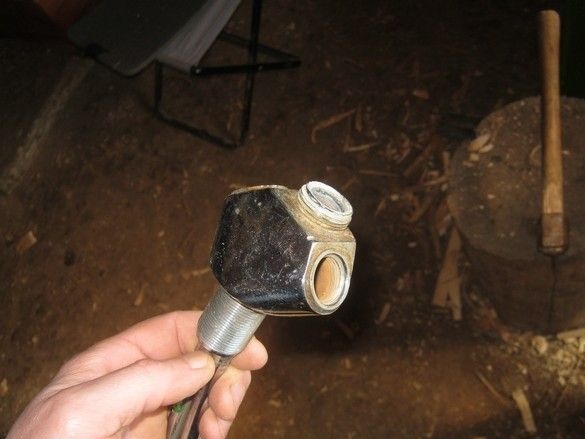
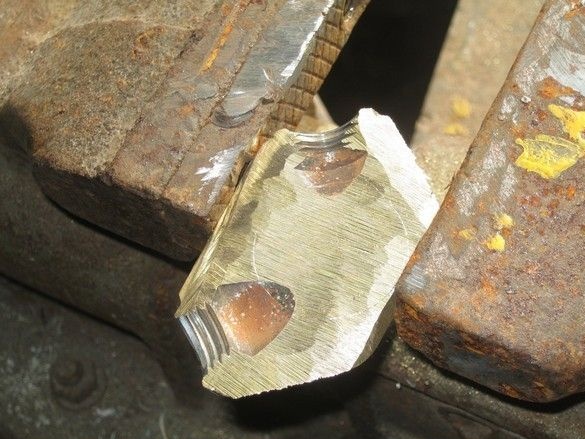
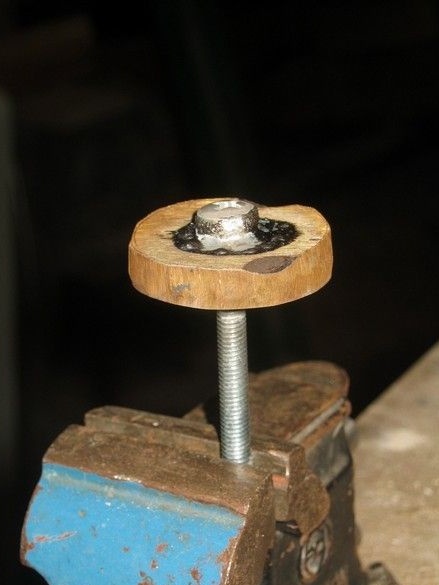
La pieza de trabajo, después de un giro brusco, se montó (soldada) en el tornillo M5, para lo cual la pieza de trabajo se podía asegurar en un portabrocas de tres mordazas para ajustar el tamaño y la forma.
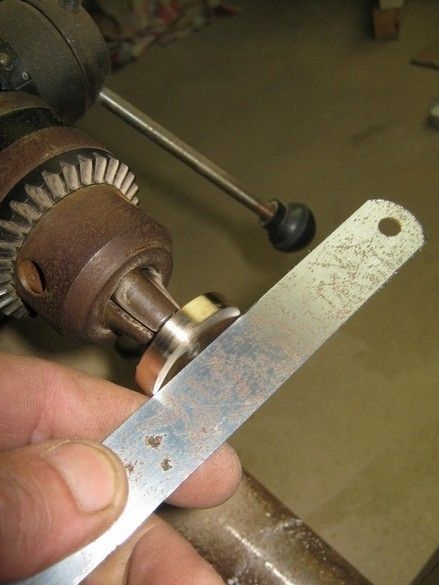
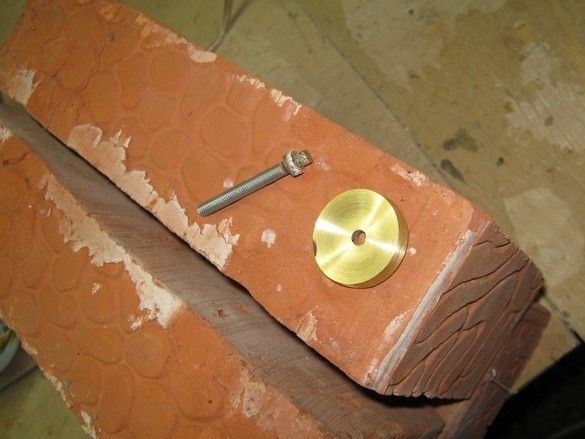
Máquina de perforación, para facilitar la operación se colocó de lado. La superficie cóncava en la pieza de trabajo se talló aproximadamente, con un pequeño "molinillo", un "remanente" del disco (menos radio), luego se trajo con una arena de molienda. El tornillo está soldado, por lo que la cabeza sobresaliente se rectificó junto con la pieza de trabajo. Después, el diámetro externo de la pieza de trabajo se llevó a la deseada. Después de girar, fundí el vástago de la pieza de trabajo, el resto del tornillo M5. El orificio restante se perforó hasta los 6 mm deseados.
La siguiente etapa responsable y bastante triste es inclinar los centros de futuros agujeros y perforarlos. Con el número correcto de agujeros y su diámetro, la tarea no es fácil. La experiencia de la radioafición ayudó mucho: perforar y perforar una gran cantidad de agujeros en las piezas de trabajo de las placas de circuito impreso, antes de la invención de componentes sin plomo (SMD), era una práctica común.
El diámetro de los agujeros ya se ha discutido, se debe decir sobre su número: su área total debe ser al menos del 20% del área de la cuadrícula.
Es conveniente dibujar agujeros en AutoCAD, entre otras cosas, este programa le permite imprimir un boceto exactamente en una escala 1: 1. Después de imprimir, la plantilla resultante se pegó a una superficie plana de la cuadrícula con lápiz de pegamento, centrándose en el orificio central, es conveniente hacerlo a la luz.
Para atornillar, utilicé un núcleo especial en miniatura. Debe cuidar una buena luz brillante, una pantalla especial con lupas es conveniente para este trabajo. El trabajo no es rápido y es importante organizar un lugar cómodo: una superficie libre, el "operador" en una posición sentada. Recomiendo hacer tales operaciones en más de un enfoque. Después de perforar, la plantilla se despega, los residuos se lavan con agua tibia.
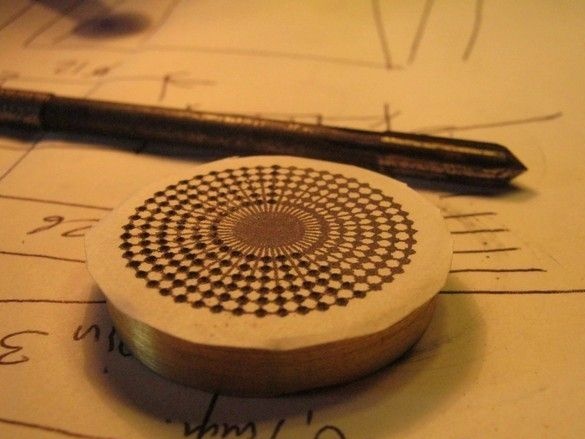
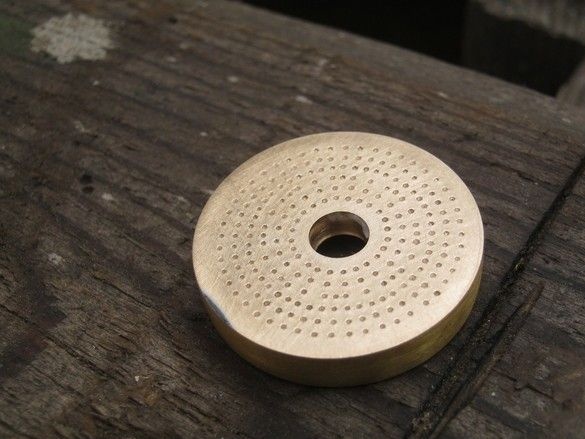
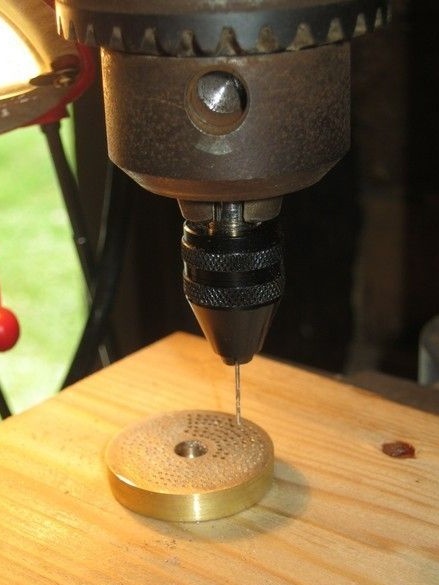
Para taladrar de este tipo: metal grueso, taladros delgados, la precisión necesaria, una variedad de dispositivos portátiles son completamente inaplicables. Deberías usar algo más estacionario. En este caso, se usó un mandril en miniatura para sujetar mi taladro de 0.8 mm; el vástago se sujetó en un mandril grande de tres mordazas en un taladro de banco. Esta combinación nos permitió perforar con confianza con un taladro delgado; rompí solo uno, e incluso entonces al final.
Resulté ser taladros baratos comprados en una tienda de radio y eran de mala calidad, una especie de simplificación de la idea de un taladro. Los surcos para la descarga de virutas en ellos eran muy poco profundos. Existe la sospecha de que están hechos específicamente para perforar láminas de fibra de vidrio y es mejor usar brocas normales de "construcción de máquinas".
Yuri Nikolayevich dice que hay casos de taladros que se atascan durante la perforación profunda, por lo que debe comprarlos con un margen y luego elegir no cuñas. Se supone que esto se debe a su reducción. La perforación es algo más fácil cuando se lubrica el taladro con aceite o alcohol, pero se debe agregar alcohol constantemente.
El afilado correcto de un taladro en miniatura de este tipo es una tarea difícil y, en ausencia de habilidad, es mejor usar nuevos taladros, de lo contrario, es inevitable un "tirón" significativo al perforar. Sin embargo, con una perforación cuidadosa en la máquina, todos los agujeros necesarios se pueden perforar con un solo taladro desde un afilado.
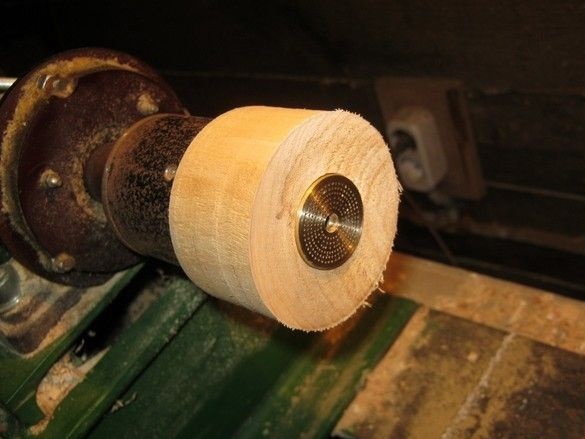
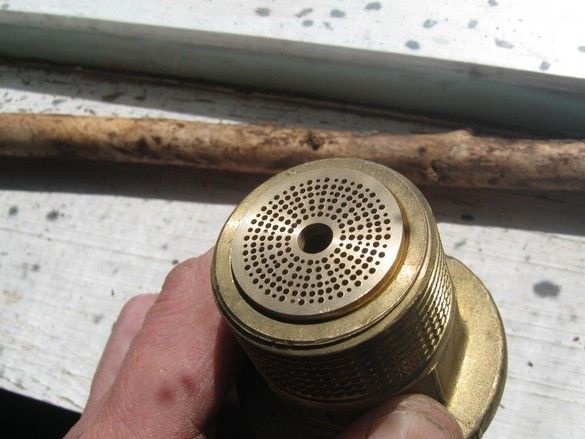
Después de perforar, se deben lijar todas las rebabas pequeñas resultantes. Esto se hace más convenientemente en una parte giratoria. Para instalar la rejilla en un torno de madera, se mecanizó el equipo más simple. La malla se ajusta perfectamente en el receso.
En la fabricación del prototipo de quemador, se suponía que solo funcionaba con vapores de gasolina, por lo que algunos de los agujeros se hicieron más grandes: 1 mm.
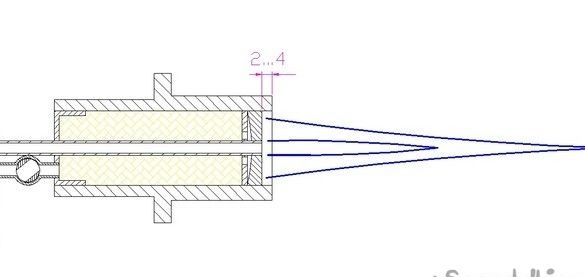
La rejilla está empotrada en el cuerpo por 2 ... 4 mm. Yuri Nikolaevich recomienda que se seleccione cuidadosamente este tamaño: si hay un exceso, el cuerpo del quemador se calentará mucho, si es insuficiente, la antorcha en algunos modos es propensa a descomponerse.
En mi caso de "baja temperatura", al alimentar solo vapores de gasolina, sin gas explosivo y con un caso muy masivo, establezco la profundidad máxima sin ajuste. Después, sería bueno soldar la malla. Esto debe hacerse con soldadura "dura". El fósforo de cobre es adecuado, pero en este caso, la soldadura de plata como PSR-45 es mejor, se quema menos. No pude soldar completamente la malla en mi caja masiva, no pude soldarla con soldadura; no había suficiente temperatura, incluso cuando la calentaba con un reflector, un soplete grande. Sin embargo, la cuadrícula entró en el cuerpo con un buen ajuste, así que lo dejé como está.
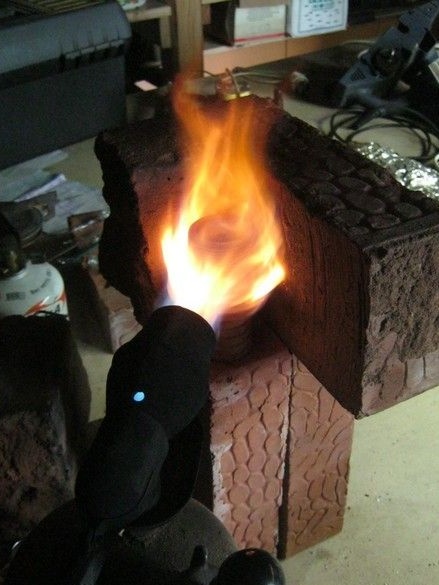
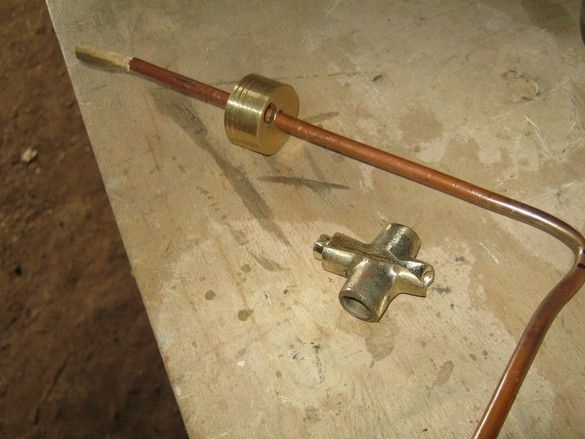
Boquilla: una simplificación completa. Hecho de tubo de cobre con un diámetro interno de 4 mm. Úselo solo como una opción de prueba. Citaré de [1] - “La boquilla debe dar un flujo laminar estrecho de la mezcla combustible y una antorcha afilada al menos con una llama baja. Su laminaridad puede garantizarse con un diámetro de orificio de hasta 2,5 mm, una longitud de más de 35 mm, una superficie interna pulida y un flujo tranquilo en la entrada. La llama laminar hace menos ruido y le permite reducir la zona de calentamiento, por lo que debe intentar obtener una antorcha laminar. (Los sopladores de vidrio profesionales pueden tener opiniones diferentes sobre este tema). La abertura de la boquilla se hace mejor cónica; esto proporcionará menos resistencia al flujo. La parte final con una longitud de unos diez milímetros debe hacerse cilíndrica ".
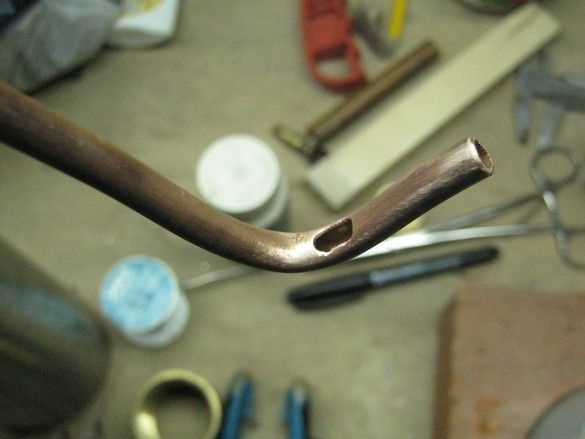
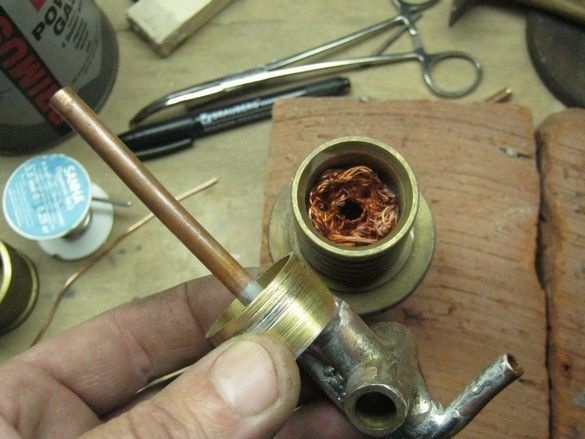
Antes de doblarse, el tubo de la boquilla se recoció y se llenó con arena seca. La cavidad interna del quemador se llenó libremente sin un fanatismo especial con un "embrollo" de cobre; esto es una protección adicional contra el "avance" de la llama y la calma del flujo de gas. El acolchado también sostiene el diafragma presionado desde el interior a la rejilla.
Todas las soldaduras "por detrás" se realizan con soldadura de estaño y cobre, con un punto de fusión de aproximadamente 200 ° C. El cuerpo del quemador se calienta significativamente, la parte de la cola no supera los 60 ° C: puede agarrarlo fácilmente con la mano e incluso después de un uso prolongado, la unidad no se colapsa.
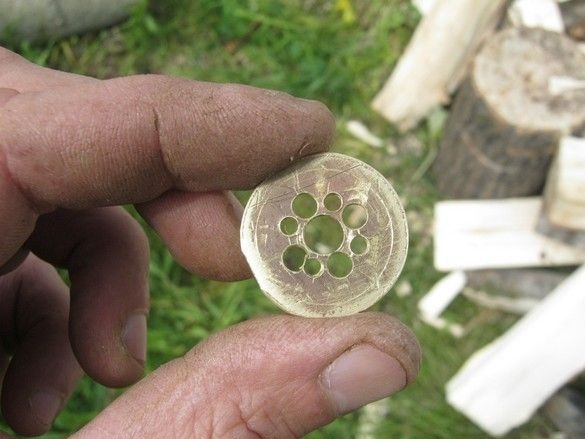
El diafragma en sí está hecho de una placa plana de latón de 3 mm. Para un efecto más pronunciado, la "lente" debe hacerse biconvexa, para lo cual el diafragma también debe ser cóncavo. Para hacer esto, se puede doblar usando Punzel y Anki, o rectificar desde una pieza de trabajo más gruesa similar a una cuadrícula.
Después de los encendidos de prueba, parecía que la antorcha era corta, como una razón probable, se vieron secciones delgadas de tubos que suministraban gas a la carcasa. El quemador se ha modernizado: los canales de grifo de corcho se perforan hasta un diámetro de 7 mm y se reemplaza el tubo de suministro común.
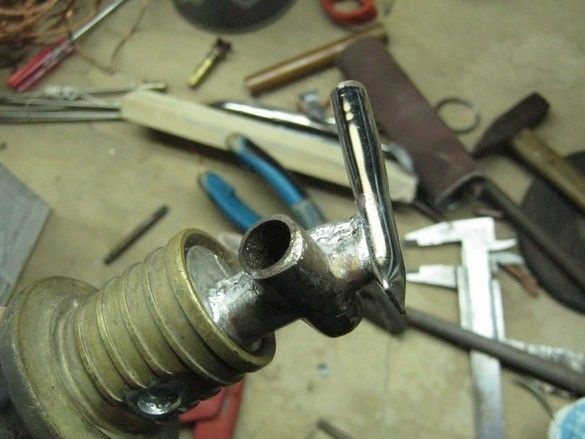
Se puso un poco mejor. Al mismo tiempo, instalé una antorcha de apoyo. Yuri Nikolayevich aconseja archivar una lima triangular de surcos, una especie de asterisco de cinco a siete rayos, en el orificio de la malla a través del cual pasa la boquilla central, para que haya una mezcla mejorada que fluya alrededor de la boquilla. Aumentará la estabilidad de la "aguja" y reducirá la pérdida en modo turbulento.
La cantidad de mezcla combustible para la llama de soporte se establece mediante los orificios en la boquilla dentro de la carcasa. Su número y tamaño son personalizables.
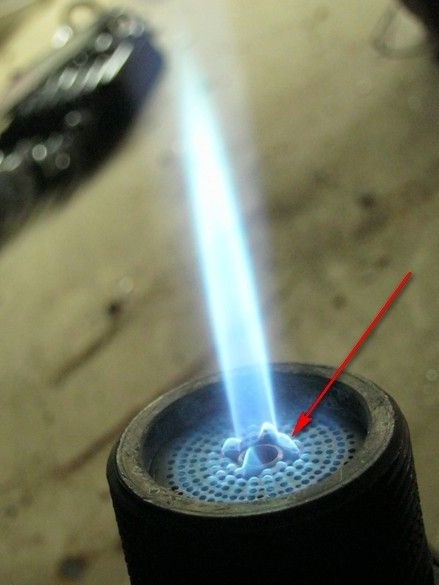
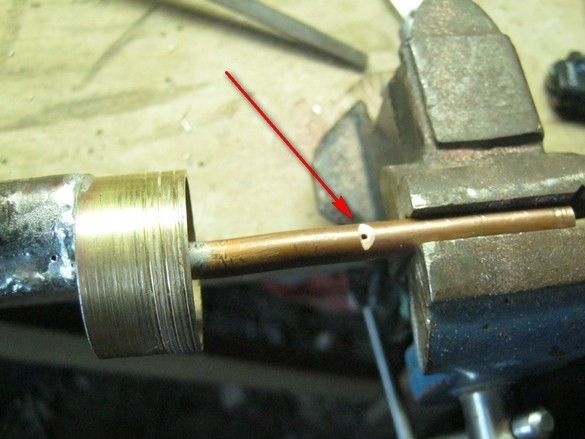
Algunas fotos de la antorcha obtenidas hasta la fecha con una posición diferente del grifo en el quemador, por así decirlo, "aguja", llama "suave" y algo promedio.
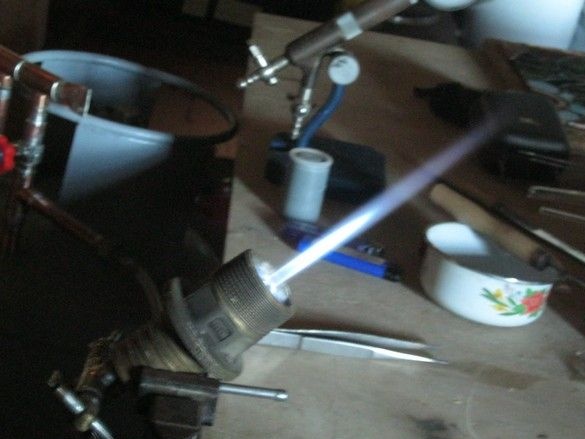
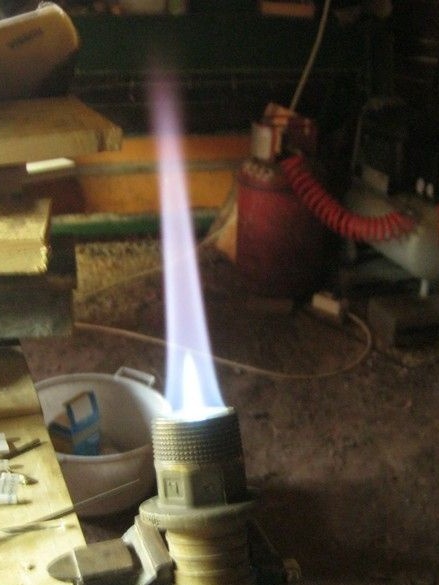
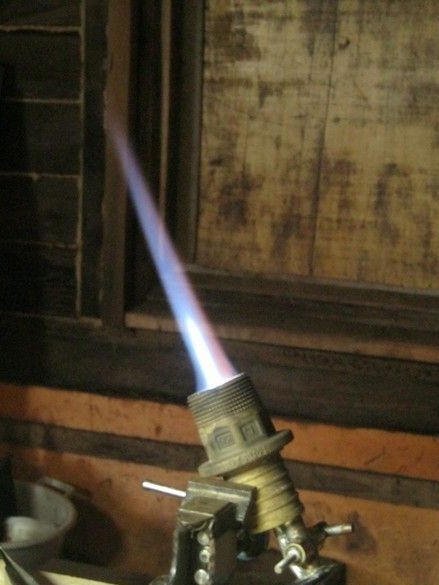
No se hizo una "pata" para el quemador experimental; durante la operación, sujetó su caja en una pequeña prensa de mesa.
La antorcha resultante es mucho más grande que el primer quemador pequeño, incluso con la adición de una hermana de gas. El vidrio se calienta mucho más rápido y un área más grande, "fluye", fue posible inflar un tubo de 18 mm de vidrio fusible de "neón". Resulta operaciones que no tuvieron éxito antes: girar los bordes y perforar una gruesa capa de vidrio con una aguja de tungsteno.Sin embargo, existe la necesidad de un aumento adicional en la temperatura de la antorcha. No hay muchas opciones: la adición de oxígeno o gas explosivo.
Trabaja en los errores. Formas de mayor mejora.
Sin embargo, este tipo de trabajo debe realizarse utilizando un torno de metal, las piezas y toda la estructura serán más precisas y precisas, lo que las hará menos dolorosas. El diámetro de la carcasa y la boquilla es obviamente demasiado grande, parece que eso es lo que no permite obtener una antorcha más larga de llama suave: la velocidad del gas al caer en una carcasa ancha (boquilla) cae significativamente. Vale la pena acercarse al tamaño del quemador en [1]. Sería bueno hacer una boquilla, un cuerpo, una malla y un diafragma con una pieza en bruto de latón, y no con nada: el diseño se puede hacer más conveniente en el montaje y el ajuste. Sería bueno hacer una boquilla de acuerdo con la carta: un agujero pulido cónico y torneado (ver arriba o [1]). Sobre oxígeno o "serpiente de cascabel", ya dicho.
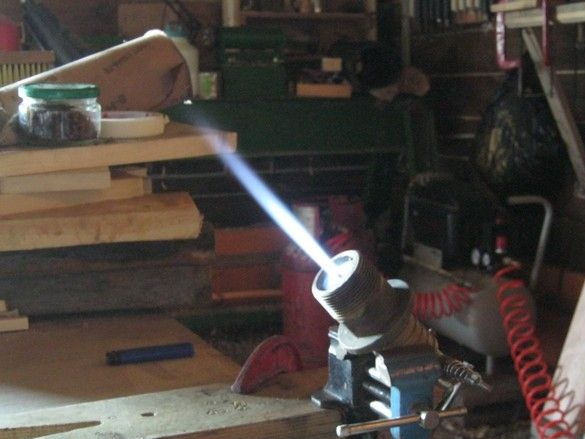
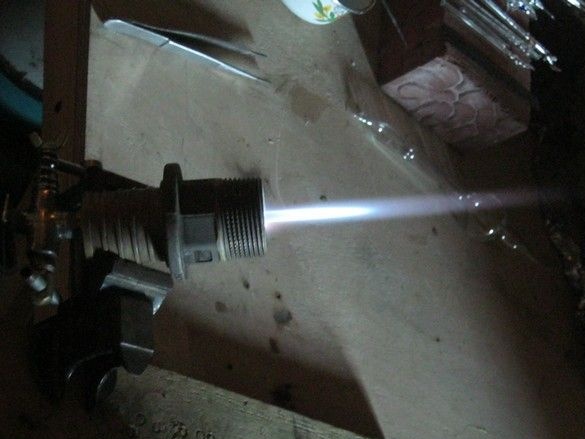

Literatura
1. Bondarenko Yu.N. Tecnología de laboratorio. Producción de fuentes luminosas de descarga de gas.
para fines de laboratorio y mucho más.