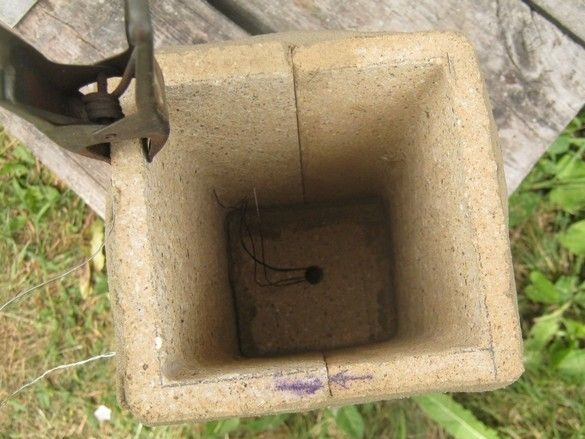
La parte más compleja y crucial de un horno de mufla de alta temperatura es, de hecho, una mufla con un calentador encima. Para la fabricación de la mufla del horno, se utilizan metales y cerámicas. Los metales hacen posible lograr una distribución de temperatura particularmente uniforme en el volumen de trabajo del horno; en algunos casos (por ejemplo, dispositivos de vidrio recocido) esto es muy importante. La cerámica se usa a menudo.
Para hornos de laboratorio especiales que operan con pequeños volúmenes de sustancias, a menudo se usan tubos de cerámica listos para usar, y solo queda enrollar y sujetar un calentador de alambre con revestimiento de alta temperatura. Habiendo equipado la mufla en miniatura con una carcasa con aislamiento térmico, obtenemos un horno especial listo para usar. Para grandes volúmenes de la cámara de trabajo, los artesanos usan un tubo de cerámica de un poderoso reóstato como mufla. Hacer un horno es similar. En un caso más general, la mufla debe hacerse a propósito. Dar a luz, por así decirlo, en agonía.
De hecho, la fabricación independiente de una mufla de cerámica, por regla general, causa dificultades: la cerámica, a primera vista y simplemente implica muchos matices, y desarrollar la tecnología es un negocio a largo plazo. Además, una mufla seca requiere asar a una temperatura alta, lo que también suele ser difícil de llevar a cabo, especialmente para las mufla, sin importar cuán grandes sean.
Propongo un método "seco" para hacer una mufla que no requiera equipo especial o habilidades de ceramista. La parte principal de la mufla es una caja de dos partes en forma de U, cada una de las cuales está aserrada de ladrillo refractario (arcilla refractaria). El espesor de la pared es de aproximadamente 10 mm. Las ventajas del método son obvias: ladrillos de arcilla refractaria, refractarios fabricados de fábrica, prensados, calcinados, todo como lo requiere la carta. La conductividad térmica de la arcilla refractaria es considerable, mucho más alta que los ladrillos de arcilla ordinarios, razón por la cual está prohibido apilar los hornos de ella: las paredes exteriores se calientan rápida y fuertemente, el horno se convierte en peligro de incendio. La arcilla refractaria en estufas de leña se usa solo para revestimiento.
Cuando se utilizan ladrillos de arcilla refractaria en blanco, se elimina toda una capa de tareas relacionadas con la cerámica, que, por regla general, se convierte en un obstáculo y una lápida de un diseño concebido.Cortar ladrillos, amoladoras angulares con un disco de diamante es una habilidad mucho más común. Al final, puedes practicar usando ladrillos de arcilla baratos. La mufla resulta ser de un tamaño bastante decente: más de 4 litros.
Lo que se usó en el trabajo.
Herramientas
El protagonista de esta acción, por supuesto, fue una amoladora angular con un disco de diamante, popularmente un "búlgaro". Taladrar agujeros en chamota (para un termopar): un perforador en el modo de perforación con un taladro convencional. Un pequeño martillo fue útil. Asegúrese de usar gafas de seguridad, preferiblemente auriculares o un tapón para los oídos. Platos para el agua. Cable de extensión (trabajo en la calle).
Materiales
Tres ladrillos de arcilla refractaria. Agua
Entonces
Al principio, debe decirse que los ladrillos de arcilla refractaria se aserran mucho peor que los ladrillos de arcilla, a veces con zumbidos y chispas. El agua ayuda mucho: al cortar, mantenga un balde de agua al lado del balde y, después de cualquier pequeño corte, riegue la pieza de trabajo con agua. Esto, entre otras cosas, elimina el polvo y las piezas de chamota, lo que le permite ver mejor el lugar de trabajo. Pero lo mejor de todo es remojar el ladrillo durante varios días en agua. Esto hace que el procesamiento sea más fácil en un orden de magnitud: la chamota se corta casi tan fácilmente como el ladrillo de arcilla; regar periódicamente el lugar de los cortes al mismo tiempo tampoco dañará.
Amoladora angular y, en consecuencia, el diámetro del disco. Por un lado, una máquina grande le permite manejar un disco grande, lo que es conveniente para realizar cortes profundos. Por otro lado, uno pequeño, con un disco de ø125 mm, permitirá trabajar en algunos lugares con una mano (no con cortes profundos), es mejor controlar la herramienta en caso de un probable atasco del disco. Pero tienes que esquivar. Sí, recordamos que el "búlgaro" es una de las herramientas más peligrosas, a diferencia de las demás, no tiene absolutamente ningún énfasis y solo debe confiar en la dureza de sus manos y la habilidad correspondiente: tenga cuidado. Sí, el ladrillo procesado debe repararse, al menos debido a las tensiones horizontales, bueno, al menos con varios listones fijados al escritorio.
El marcado se puede hacer tanto en ladrillo seco como después de remojar.
Doy una secuencia de mis propias acciones, para una herramienta con un diámetro de hoja de sierra de 125 mm.
Algunos cortes en el medio del ladrillo a la máxima profundidad posible. A una distancia de 5 ... 7 mm entre sí. Es mejor cortar para que la línea de marcado esté afuera. El ladrillo da vuelta y las acciones se repiten.
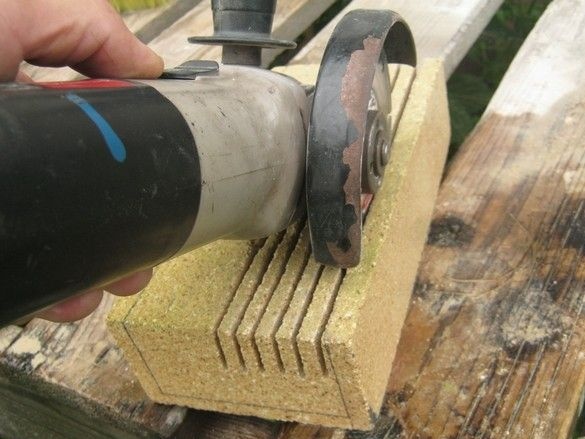
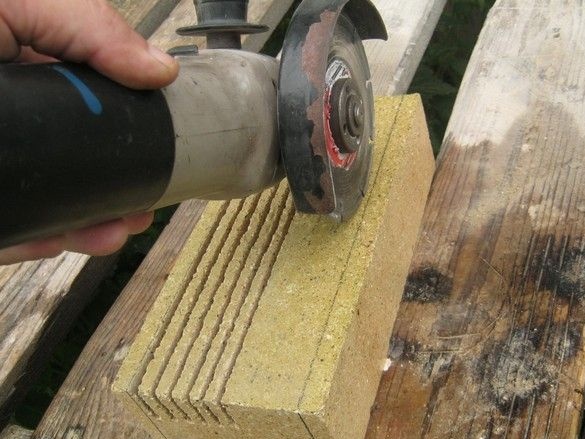
Después de completar los cortes, el ladrillo en blanco debe lavarse con agua y proceder a la extracción del núcleo. Manejó la palanca: la llave de la amoladora angular salió bien, pero también fue posible con un martillo. Por lo tanto, no vale la pena romper el diente más cercano a la pared izquierda: la pared exterior es ligeramente más gruesa que la que se está rompiendo, nunca se sabe, es mejor tener cuidado con un martillo.
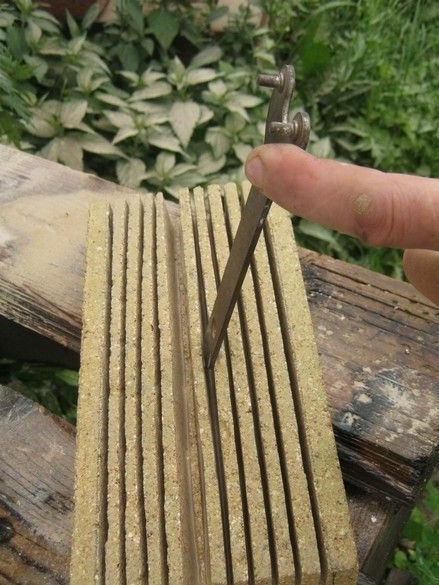
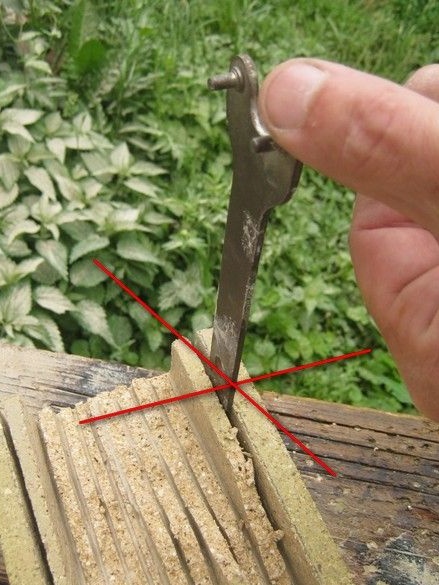
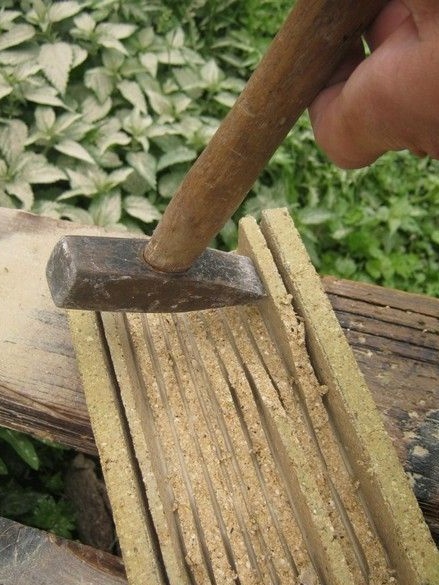
Lavamos los escombros, fragmentos y cortamos a través del segundo nivel, de la misma manera. Por desgracia, la carcasa de la caja de engranajes de la máquina no permite llegar al centro, debe cortarse con cortes oblicuos. Aquí, en cada corte se forma mucho polvo (y en ladrillos empapados, en lugar de suciedad) y pequeños restos, por lo que debe regarlo cada hora.
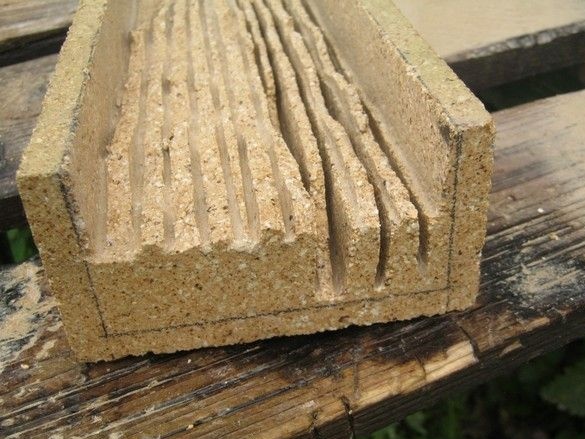
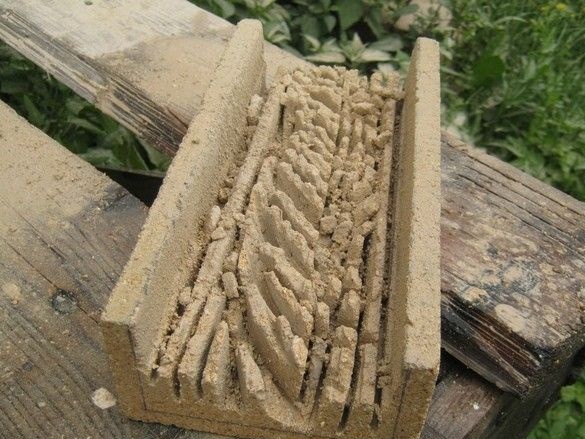
Después de noquear los dientes, hay muchas irregularidades que también deben alinearse, pero no con cortes normales,
y con largos movimientos laterales de la máquina, aproximadamente para que funcione la superficie lateral del disco de diamante. No te olvides del agua.
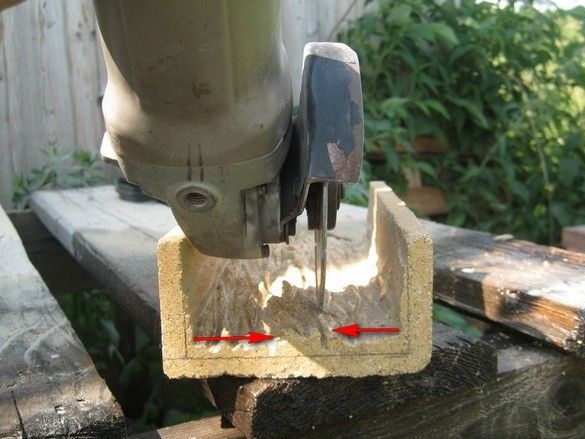
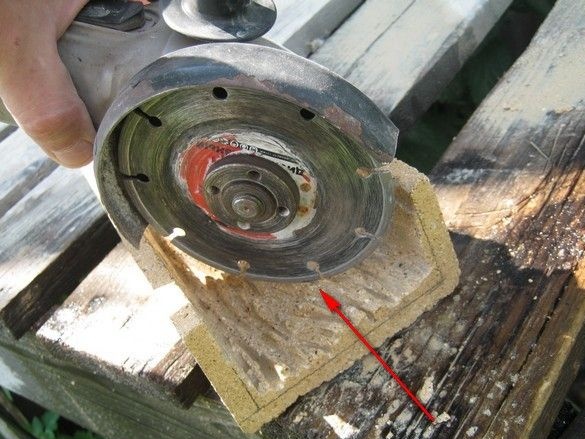
El orden, había engrosamientos en las esquinas, tenían que ser elegidos de manera un poco diferente, y resultó que no había forma de entrar en el disco. El problema se resolvió reemplazando un disco desgastado por uno nuevo; los 5 ... 7 mm faltantes eran suficientes.
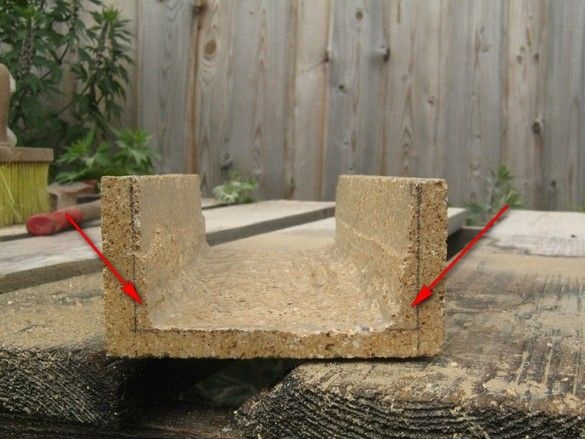
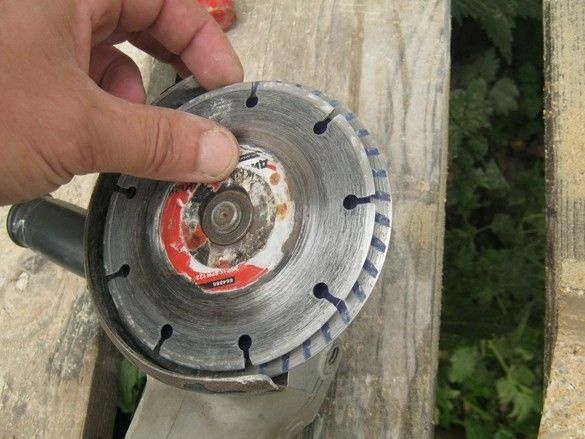
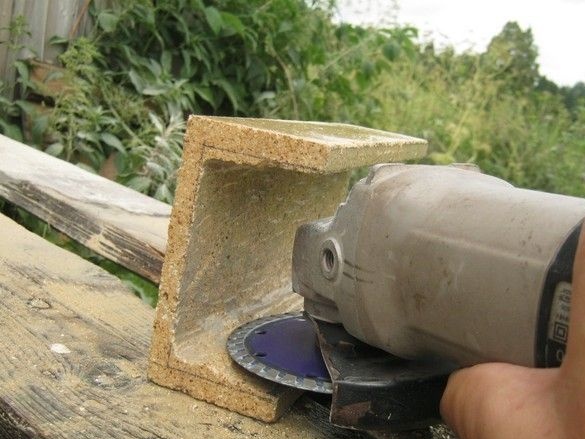
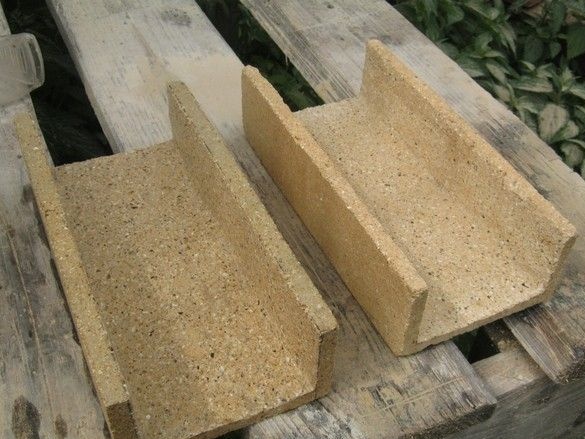
Después de tales esfuerzos, para cortar el fondo, un trabajo insignificante, se cortó una placa de 20 mm de espesor de ladrillo, se hizo un "cuarto" de 10 mm de profundidad alrededor del perímetro. En estos 10 mm, la parte inferior se inserta en el cuerpo de la mufla.
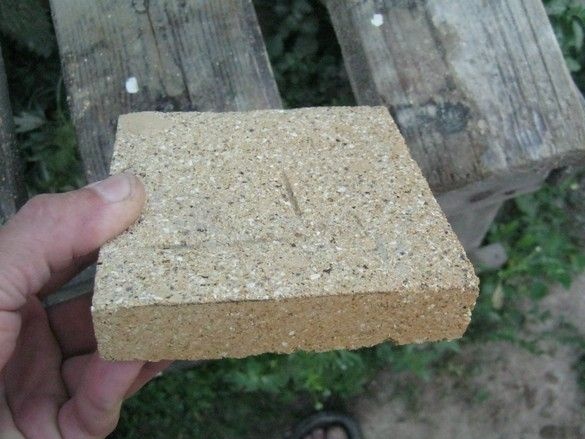
Se perforó un agujero de ø10 mm en el fondo para un termopar. Como ya se mencionó - taladro de carburo (taladro).
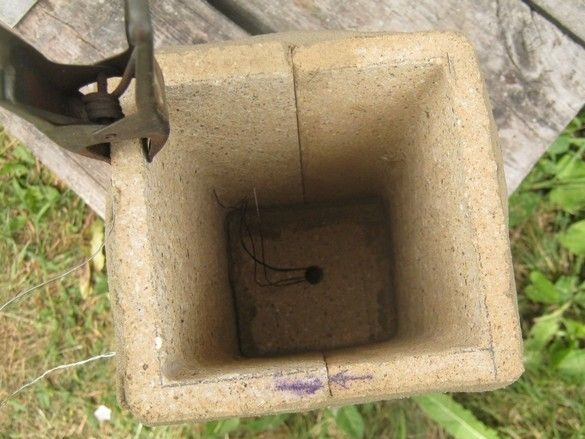
Aquí se aplicó la composición para la colocación de ladrillos refractarios "terracota".
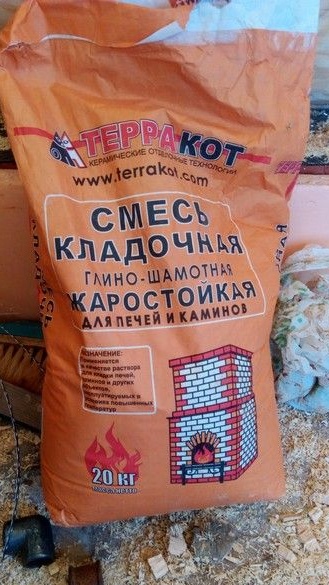
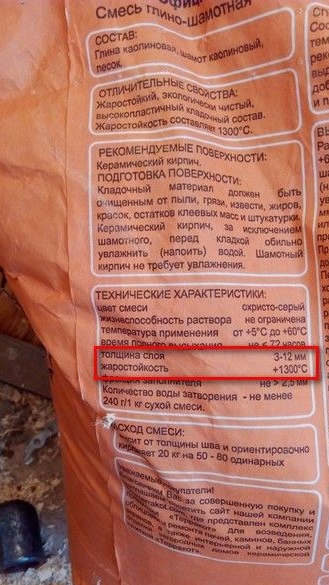
Es probable que una capa de 12 mm sin grietas produzca la mufla solo con esta composición.
La mezcla diluida con agua es muy conveniente en el trabajo, fue necesario usarla para colocar el revestimiento de arcilla en una estufa de leña.Aquí, la parte inferior de la mufla está instalada, la mezcla también se usa para recubrir el calentador. Las mitades en forma de U no se pegaron: todavía habría una grieta durante el calentamiento-enfriamiento, además, las mitades fueron muertas por un fuerte enrollamiento de un calentador de alambre. De hecho, el fondo tampoco tenía que estar pegado, un ajuste apretado era suficiente. La costura inferior también se rompió más tarde, pero ¿qué pasa?
Conclusiones, observaciones generales
El corte, que parecía más terrible que las aspiraciones, no era en absoluto gravoso, sino con remojo a fondo (durante varios días) de ladrillos, y en algún lugar una ocupación agradable. La mufla resultó, según los estándares de los hornos de alta temperatura, de tamaños bastante decentes. Si es necesario, un volumen más pequeño (horno especializado, por ejemplo, para trabajos de lámpara), puede tomar un "canal", bloqueándolo con una placa.
La temperatura de uso de la mufla cuando se usa un calentador de alambre de nicromo es de hasta 950 ° C, y cuando se usa fechrales, es ligeramente más alta. En este último caso, debe recordarse que no está permitido el contacto del fechral con el asbesto.
No hay una cubierta especial en esta mufla: estará hecha de cartón de asbesto, como una puerta horno en miniatura.
El trabajo descrito anteriormente con una herramienta eléctrica con ladrillos de perforación afilada reduce significativamente sus recursos: polvo abrasivo, motores de conmutación. Es muy útil después de este trabajo no ser demasiado flojo para soplar los taladros de la amoladora con aire comprimido, incluso sin desmontarlos, a través de aberturas regulares en el estuche.
En la foto, una mufla con un calentador y bobinado de asbesto, extraída para su inspección, después de un mes de operación.
