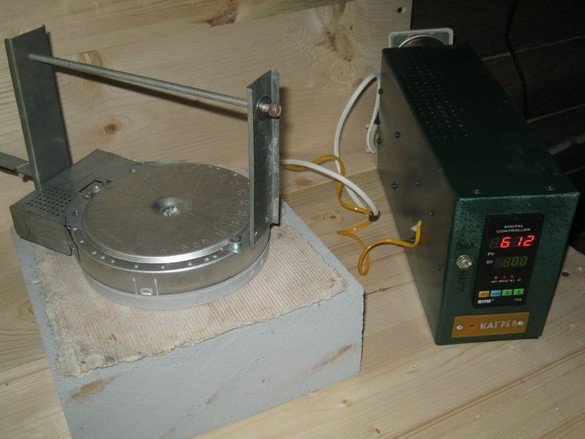
La fusión, (ing. Fusión de fusible - sinterización, fundición) es relativamente reciente. costura y como lo es ahora, nació en 1990. Aparentemente, la fabricación de un vitral "sinterizado" se hizo posible con la llegada del vitral con igual KTP (coeficiente de expansión térmica). Se hace así: sobre una base de vidrio, se presenta un patrón de piezas de vidrio de colores, y sus bordes, en la mayoría de los casos, no requieren un ajuste y procesamiento precisos, suficiente corte de vidrio y pinzas especiales. La preforma ensamblada se coloca en un horno especial y se calienta a la temperatura a la que se derrite el vidrio.
La vidriera resultante se ve muy peculiar: bordes redondeados lisos, cada elemento se asemeja a una especie de caramelo derretido. Con un poco de habilidad artística, obtenemos artilugios muy interesantes. Además, aquí puede aplicar todo un arsenal de técnicas: use papel de aluminio, aserrín, alambre, plantillas para ellas, técnicas de esmalte cloisonné, aplique pinturas de cocción sobre vidrio y cerámica, productos químicos que producen burbujas dentro del vidrio. El horno de fusión también permite el moldeo de vidrio plano - doblado. Los artefactos terminados se pueden combinar con métodos de "baja temperatura", en grandes vitrales. En una palabra: un abismo de oportunidades para la creatividad.
El vidrio coloreado, con el mismo CTE, como muchos materiales para fusión, es costoso, sin embargo, el artículo más costoso para dominar esta técnica es, por supuesto, el horno. Un horno para fusionar vidrios es bastante inusual, su forma está dictada por la tecnología de sinterización: una mesa plana, sobre la cual es conveniente colocar una hoja de vidrio en blanco, una tapa con bisagras con calentadores. En general, se asemeja a una maleta, en algunos, incluso hay sujetadores.
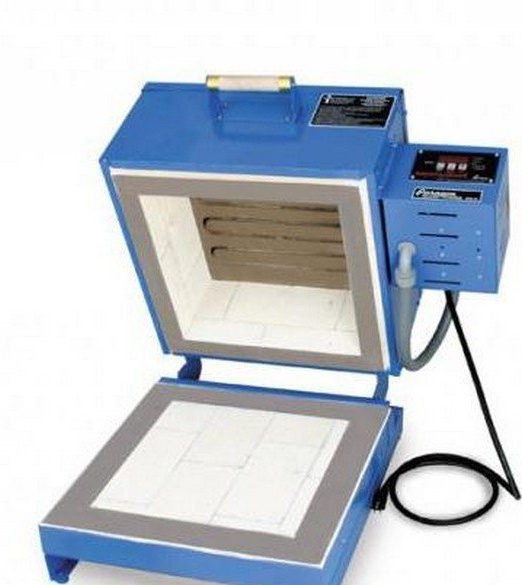
Los hornos de mufla, con un calentador en la parte superior de la cámara de mufla, no se usan, después de calentar el vidrio hasta el punto de fusión, el producto debe enfriarse bastante rápido a la temperatura de recocido, mientras que los hornos a menudo se abren ligeramente. Es difícil una caída rápida de la temperatura en la mufla: la inercia térmica es demasiado alta y es inconveniente colocar los espacios en blanco en la cámara.
Hornos para fusión, hay tamaños muy diferentes, respectivamente - capacidades. Con los calentadores de una pequeña estufa, el cableado de la casa puede funcionar bien.
Vidrio sinterizado "para no caro".
Puede probarse en este interesante negocio sin gastar grandes sumas de dinero: para empezar, hay una versión original con Ali Express: crisoles especiales para el microondas. Es un crisol refractario con revestimiento de grafito en el interior. El revestimiento se calienta en ondas de microondas y calienta el vidrio con radiación. Hay una virtud, pero una cantidad justa: el costo. Al momento de escribir, el crisol cuesta 2-4 mil rublos. Dependiendo del tamaño.
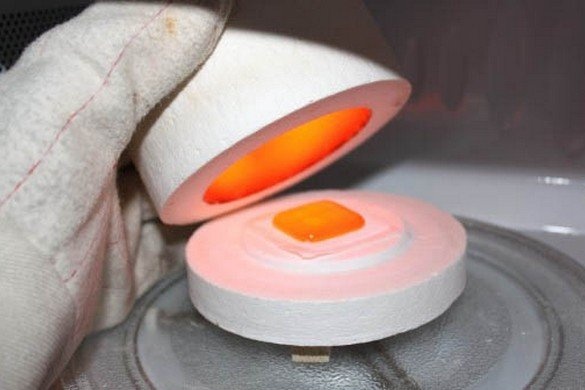
Las desventajas de una opción tan simple, como de costumbre, son masivas. La temperatura puede controlarse solo visualmente, "a simple vista", el recocido controlado para aliviar el estrés interno es imposible. Tamaño pequeño: solo para joyas, la incapacidad de usar metales. Como regla general, después de haber seleccionado experimentalmente el modo de sinterización y haber consumido los fragmentos de vidrio incluidos en el kit, se arrojan la ocupación y el crisol.
Un horno eléctrico especializado, por supuesto, es mucho más perfecto, sin embargo, el más pequeño, 200x200 mm, cuesta 35 mil rublos. Por supuesto, solo refractarios, un controlador con un perfil térmico, cuarzo y tubos de cerámica para calentadores, montaje de nuevo ... Tener un taller o garaje, un poco de metalurgia y experiencia con electricidad, es muy posible ensamblar ese horno usted mismo, gastando menos de la mitad del costo de los materiales , pero ¿qué hacer los residentes sin caballos de garaje de la "jungla de hormigón"?
Idea.
La idea de un horno de fusión extremadamente simple y económico de características "intermedias" pertenece a camarada "Ilya MSU", del foro de metal. El horno es de tamaño pequeño, pero ya es posible hornear el vidrio, mucho más serio que los colgantes de broche de anillo en el microondas. Puede usar alambre, papel de aluminio y todo el arsenal de técnicas de fusión. Calentador de resistencia eléctrica en la tapa, termopar con un controlador de temperatura simple. Baja, incluso para una potencia de apartamento, la capacidad de fabricar en la cocina a partir de piezas y elementos de bajo costo generalizados. El diseño no contiene refractarios especializados de alta temperatura.
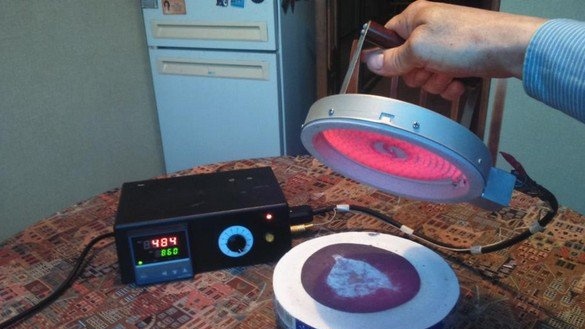
Como cubierta superior del horno de maletas, se utiliza una parte de una estufa eléctrica con una superficie de vitrocerámica: un quemador. Tiene una carcasa metálica revestida con material refractario fibroso, en el que se forman protuberancias especiales de la cinta calefactora. El quemador se complementa con un mango y un termopar conectado a un controlador simple. Como base, se utilizó una lata plana llena de yeso.
Versión propia de una estufa de quemador simple.
Tengo dos quemadores de segunda mano con un diámetro interno de "trabajo" de 140 mm, con un termostato mecánico en una caja de metal (hay opciones con un tubo de cuarzo).
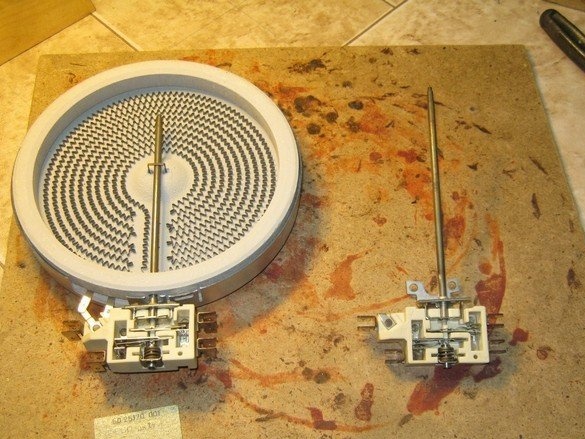
Lo que se usó en el trabajo.
Herramientas, dispositivos, equipos.
Un conjunto de herramientas de banco de tamaño mediano, una sierra de calar con accesorios, una amoladora angular pequeña, un destornillador o un taladro eléctrico. Un conjunto de herramientas de cableado, un soldador de 40 W para cableado, más grande - 60 ... 80 W - para soldadura estructural. Herramienta de marcado. Herramienta útil para instalar remaches ciegos, construir secador de pelo.
Materiales
Además de los quemadores, necesitaban láminas de asbesto, ladrillos de hormigón celular, cables diferentes, un termopar, termotubos y abrazaderas de nylon. Se usó una unidad de control preparada para un horno de mufla (o un controlador + relé de estado sólido + radiador + caja). Resistencia de extinción de potencia adecuada (calentador de aceite). Un poco de sujetadores de acero galvanizado.
Los contactos del termostato del quemador se cerraron a la fuerza y se soldaron, soldadura de estaño y cobre a los terminales de salida, se soldaron cables con aislamiento de silicona. Al lado del termostato, se perforó un agujero en la cavidad interna, se introdujo un termopar de cromo-alumel (tipo K), desde un multímetro. A la sonda del termostato estándar, el termopar adjunta varias vueltas de alambre de nicromo.
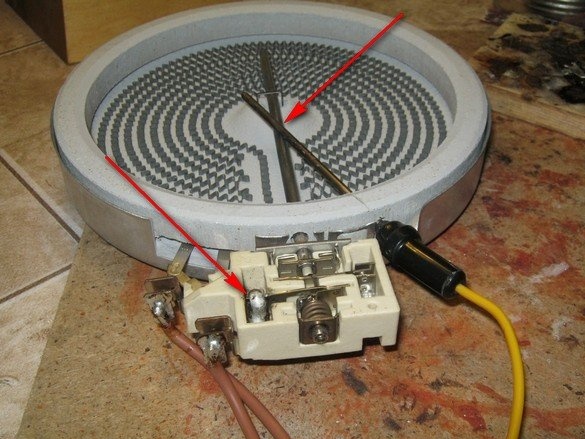
Cubierta de estaño - De hecho, resultó ser el elemento más difícil de mi horno. Se suelda a partir de acero galvanizado de "techo" de 0,5 mm, soldadura de estaño y cobre (el punto de fusión es mayor que el de las soldaduras de plomo). Flujo - ácido de soldadura (cloruro de zinc), soldador de 60 vatios.Las piezas complejas se cortaron con una sierra de calar, cortes rectos, con tijeras de metal. Las líneas curvas se marcaron así: la pieza de hierro se colocó en el lugar correcto, y con un par de brújulas, con una aguja en el centro del quemador, dibujé el radio necesario para el arco.


Soldado desde el interior, principalmente por estética. Enfrente de los terminales de "cuchilla" del termostato del quemador estándar, con cables soldados a ellos, se hicieron orificios de ventilación (arriba y abajo) en la carcasa para que se enfríen con una corriente de aire y la soldadura no se derrita.
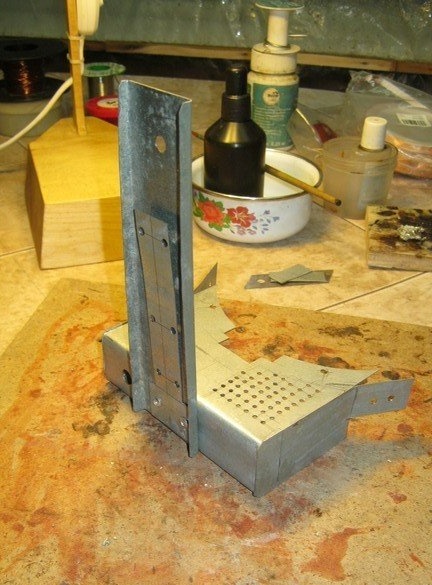
Sobre el borde de la carcasa, decidí enganchar y uno de los soportes para el mango, con los mismos sujetadores, fijó un soporte de alambre. Piezas de estaño sujetadas con remaches ciegos de aluminio.
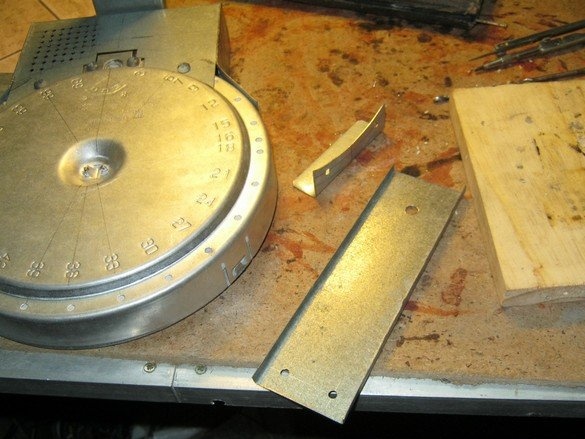
El soporte frontal para el mango se montó en una carcasa normal y consta de dos piezas de estaño. Se fija a la carcasa con tornillos cortos autorroscantes, la conexión entre ellos está remachada.
La parte exterior
El calentador del quemador, con una potencia de 1200 W, es demasiado potente para hornear vasos: la velocidad de calentamiento es excelente para un volumen tan pequeño, el vidrio no tiene tiempo para calentarse uniformemente, la pieza de trabajo se rompe. Para eliminar el inconveniente, la potencia del calentador tuvo que reducirse, para activar una poderosa resistencia en serie con él, un calentador de aceite a la mitad de potencia. Al mismo tiempo, en el calentador del quemador, la caída de voltaje es exactamente la mitad del voltaje de la red: 110 voltios.
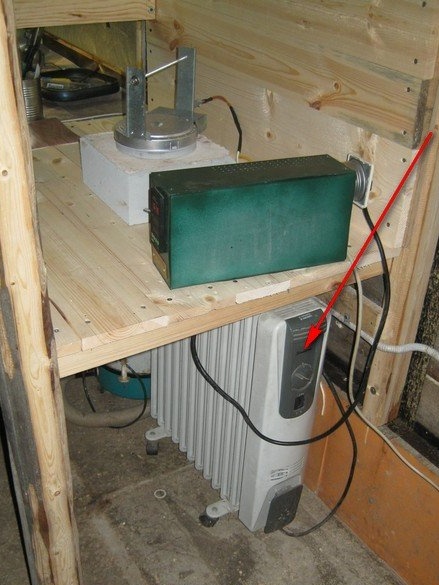
Controlador para controlar el horno. Un enchufe para la conexión y un bloque de terminales de tornillo para el calentador del horno están montados en su pared posterior. El termopar está conectado directamente al controlador.
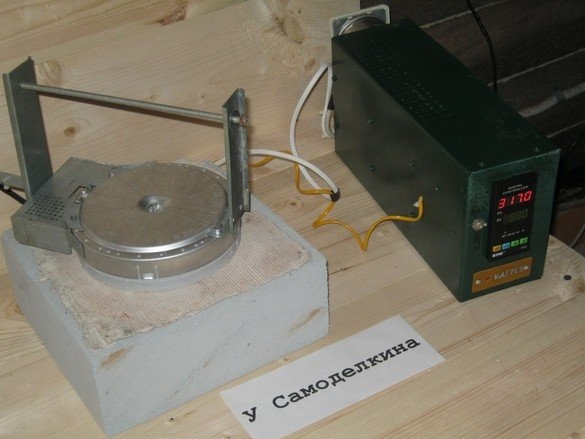
La tapa del horno es refractaria: lámina de amianto, debajo de la cual la mitad del ladrillo está hecha de hormigón celular. Cerca de allí, vale la pena mantener el mismo revestimiento resistente al fuego: sobre él, si es necesario, puede colocar la punta caliente del horno "abierto".
Sinterización
Al sinterizar vidrios, se deben mantener dos temperaturas principales: el comienzo de la fusión del vidrio (710 ... 800 ° С dependiendo del tipo de vidrio) y la temperatura de recocido (500 ... 600 ° С dependiendo del tipo y tamaño de la pieza de trabajo). El calentamiento inicial ocurre lo más suavemente posible (dentro de límites razonables, por supuesto), después de lo cual la temperatura cae rápidamente a "recocido".
Típicamente, el proceso es controlado por un controlador programable "con perfil térmico". Aquí, se aplica un controlador simple, que mantiene una temperatura, y se cambian manualmente, un dispositivo semiautomático. Al llegar a 800 ° C (~ 30 min.), La tapa del horno está entreabierta, se colocan 500 ° C en el controlador y el producto se recoce durante 1 hora. Después de eso, los calentadores del horno se apagan y el producto se enfría con el horno a temperatura ambiente (~ 1 hora). Los tamaños pequeños de vidrio le permiten no temer pequeñas imprecisiones en el proceso.
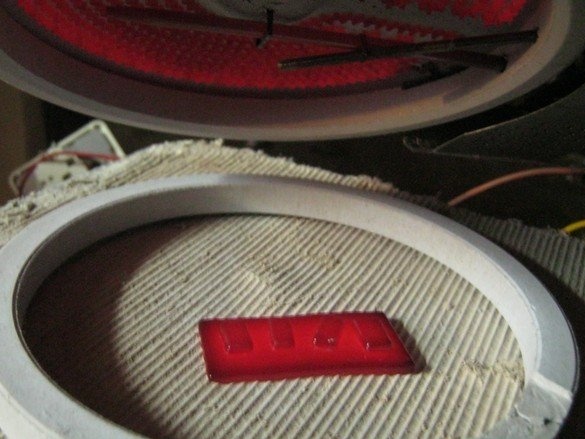
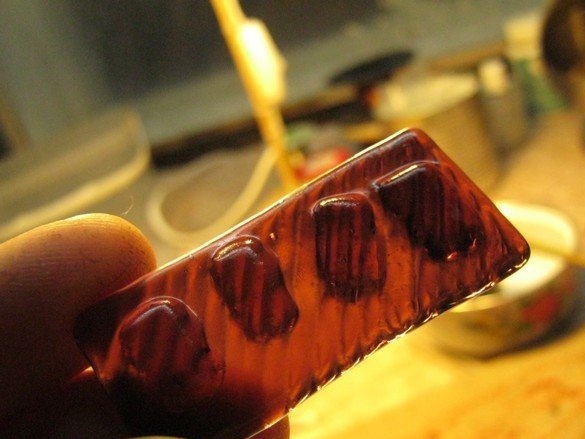
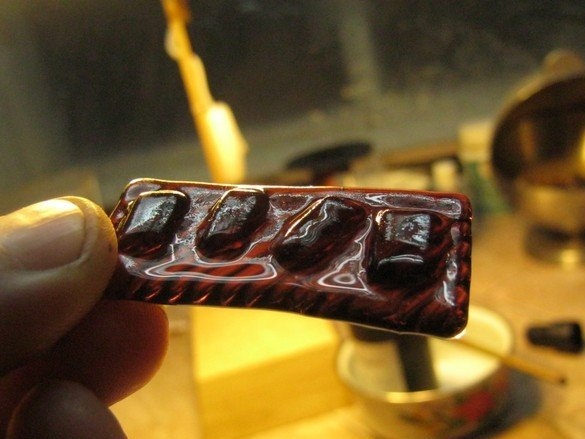
Bueno, el primer experimento es bastante exitoso: los vidrios se fusionaron, pero no en una superficie plana, la muestra no se agrietó; el perfil de temperatura para este tipo de vidrio debe considerarse exitoso. Intentemos ser más significativos.

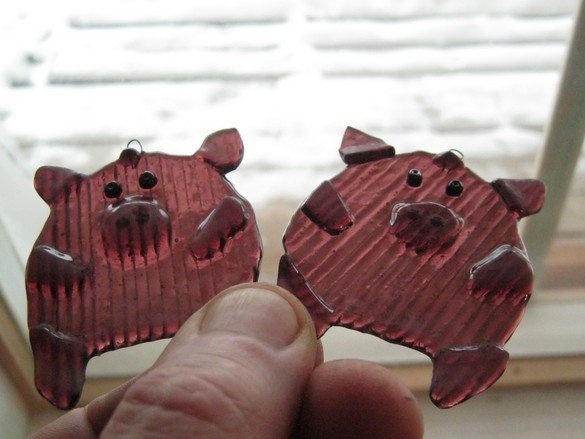

Dos bestias, hmm, bastante en el espíritu del día, como los osos olímpicos, al mismo tiempo ... Aquí, como experimento, se fusionaron dos variedades de cuentas, alambre de cobre, vidrio fundido no solo "vuelta" sino también prácticamente "de punta a punta". Las cuentas (vidrio con un KTP diferente) y el alambre de cobre (aún más) deben ser muy pequeños (diámetro, sección transversal) en relación con el vidrio principal, entonces las tensiones resultantes no destruirán el producto.
Babay Mazay, diciembre de 2018