En mi tiempo libre, a menudo hago lo que más me gusta: diseñar varias estructuras electrónicas y, por supuesto, para obtener un dispositivo completo, solo necesitas un dispositivo listo electronica el circuito (una placa de circuito impreso con componentes de radio, cables, etc.) debe colocarse en un hermoso estuche terminado que protegerá el dispositivo de factores negativos externos y deleitará la vista del propietario durante muchos años.
Creo que muchos radioaficionados están de acuerdo conmigo en que es posible producir un diseño radioelectrónico, por supuesto, dependiendo de la complejidad, en un par de horas, pero a menudo es muy difícil encontrar una vivienda ya hecha, y se pierde un tiempo valioso buscándolo. Por supuesto, siempre es posible comprar una caja terminada, pero es dinero, tiempo y no siempre calidad. Por lo tanto, decidí que sería más rápido y más confiable hacer los estuches para mí con los tamaños requeridos y de varios materiales disponibles. Para este propósito, fui concebido como una mini sierra circular de un taladro eléctrico, como una opción con el menor costo.
Materiales:
- madera contrachapada de 12 mm;
- madera contrachapada de 5 mm;
- una abrazadera para sujetar tubos Dy = 32;
- Horquilla M16 de 200 mm de largo;
- hoja de sierra (diámetro interior 16 mm, exterior 62 mm, espesor 0,8 mm);
- rodamientos 6000 RS (26 × 10 × 8 mm)
- tornillo M8 × 35;
- tornillo M4 × 25;
- frutos secos - "oveja" M4;
- M16 nueces;
- arandelas;
- tornillos autorroscantes;
- Tablero de fibra de 5 mm.
Herramientas:
- taladro eléctrico (la base de toda la máquina);
- destornillador
- rompecabezas
- cuadrado
- un lápiz
- taladros.
Instrucciones paso a paso sobre cómo hacer una mini sierra circular con un taladro eléctrico.
La granja encontró una pieza de madera contrachapada de 12 mm, que se utilizó para fabricar los componentes de la máquina. El uso de aglomerado o una tabla de madera también es posible, la única pregunta son las preferencias, la facilidad de procesamiento y la disponibilidad de este material.
Después de estimar la ubicación del taladro eléctrico, los bastidores y el escritorio, realicé el diseño de los componentes en una hoja de madera contrachapada y la corté con una sierra de calar eléctrica con una sierra de dientes finos para evitar grandes astillas.
La base de la máquina resultó con dimensiones de 190 mm × 355 mm.
Para combinar los ejes del taladro eléctrico y el eje en el que está montada la hoja de sierra, pegué un área adicional de restos de madera contrachapada de 5 mm y madera contrachapada de 12 mm con dimensiones de 175 mm × 190 mm a la base. Para mayor resistencia, la estructura resultante se juntó en las esquinas con cuatro tornillos autorroscantes, con agujeros previamente perforados de menor diámetro para tornillos autorroscantes.
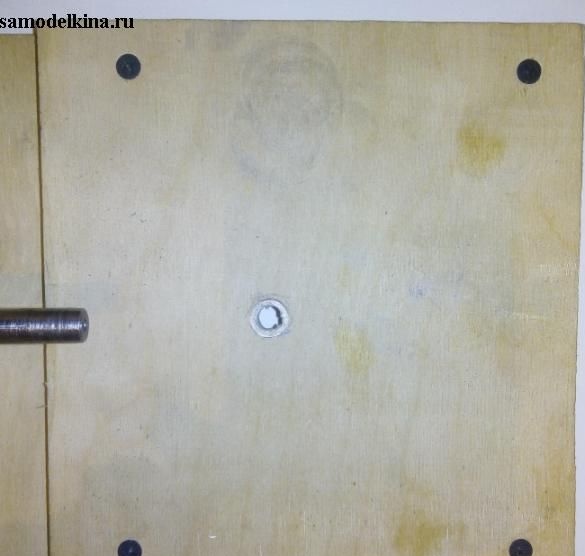
El taladro eléctrico se fija a la estructura con una abrazadera de tubo Dy = 32. Esta abrazadera en la unión con el pasador de montaje tiene una rosca interna M8, por lo que la abrazadera está unida a la base con un tornillo M8 × 35 (la longitud del tornillo, por supuesto, depende del grosor de la base con la almohadilla).
Se cortaron bastidores en la cantidad de 2 piezas de madera contrachapada de 12 mm con dimensiones de 67 mm × 190 mm. Dadas las características de diseño del montaje de la hoja de sierra, realicé la marca del centro del futuro agujero: resultó 85 mm horizontalmente y 18 mm verticalmente. Perforé un agujero con un taladro con un diámetro de 26 mm. El diámetro del taladro se seleccionó en función del diámetro exterior del rodamiento.
Después de perforar un agujero para el rodamiento, resultó que su tamaño es de 26.5 mm. Como no tengo una máquina de perforación o soporte para un taladro, lo taladré con un taladro eléctrico manual, por lo tanto, lo más probable es que la diferencia fuera de 0,5 mm, y esto ya era demasiado para encajar el rodamiento con interferencia. Salí de la situación de manera muy simple: utilicé tiras de metal de 0,35 mm de grosor para sellar el rodamiento en el orificio. Las tiras se cortaron con un ancho de 12 mm en el grosor de los montantes y una longitud igual a la circunferencia del rodamiento en el diámetro exterior. Después de este procedimiento, los rodamientos se colocaron en su lugar con un ajuste de interferencia simplemente hermoso. Quizás este procedimiento deba proporcionarse por adelantado, en caso de que alguien quiera repetir este diseño.
Inicialmente, se decidió colocar rodamientos con el nombre 6000 2RS (en nuestro el modelo 100) con un diámetro interno de 10 mm para aterrizar en un eje, que luego se puede sujetar convenientemente a un portabrocas eléctrico (el diámetro máximo del portabrocas es de 13 mm). Estos rodamientos son de tipo cerrado, lo cual es importante: no se acumulará polvo fino.
El eje para aterrizar la hoja de sierra es quizás la parte más difícil y crítica de mi máquina. Dado el hecho de que obtuve la hoja de sierra absolutamente libre de un amigo y no la elegí, aquí es de donde provienen las dimensiones del eje futuro.
La horquilla M16 se seleccionó por el diámetro del asiento de la hoja de sierra. A continuación, es necesario moler debajo de las dimensiones del asiento del rodamiento (10 mm) desde uno y el segundo lado del espárrago. En el lado donde se fijará el eje en el portabrocas eléctrico, en un torno, rectificar 60 mm, en el segundo lado es necesario rectificar en el ancho del rodamiento disponible, diseñé 10 mm para mayor precisión. Muchos argumentarán que trabajar en un torno no es asequible para todos y este procedimiento requiere habilidades especiales, por lo que el juego no vale la pena, pero quiero convencer a todos de lo contrario. Los costos de fabricación de tal eje están completamente nivelados por la estabilidad de la máquina (la vibración es escasa, la precisión de corte es alta). Tampoco tengo un torno, ni las habilidades para trabajar con él (aparte de la práctica tecnológica en una universidad), pero un cerrajero familiar me mecanizó un eje a un precio simbólico (alrededor de $ 1), porque la pieza no es difícil de realizar. Como dicen, ¡todo está en sus manos, caballeros!
La hoja de sierra, como escribí anteriormente, me liberó por completo, con un diámetro externo de 62 mm, un diámetro interno (debajo del asiento) de 16 mm y un grosor de 0.8 mm. De dientes finos: no contaba la cantidad de dientes. Un pequeño espacio entre dientes evita que el material de corte se enganche en la hoja de sierra. Habiendo estimado la ubicación de la hoja de sierra en el eje, la configuré correctamente (la alineación principal) y la sujeté con dos tuercas M16.
Una mesa de trabajo de 190 × 250 mm está hecha de madera contrachapada de 5 mm. La longitud de la ranura para la hoja de sierra está determinada por su diámetro. Lo hice un poco con un margen: 75 mm de largo y 5 mm de ancho. Propyl hizo una sierra de calar eléctrica. No tengo que cortar pequeños detalles, como para el modelado, por lo que este corte fue óptimo para mí, aunque un ancho de corte de 2 mm en mi caso sería suficiente. Las dimensiones de la mesa de trabajo deben seleccionarse según la conveniencia de montar el eje de la máquina en el portabrocas eléctrico.
Asamblea
Cada puntal con rodamientos prensados se fijó a la base con tres tornillos autorroscantes gruesos (5 mm) para traicionar la estructura de rigidez. La distancia entre los montantes fue de 138 mm (axial). El escritorio se fijó en 4 tornillos autorroscantes (3,5 mm). Orificios naturalmente pretaladrados de menor diámetro para evitar la delaminación de la madera contrachapada
Como guía, utilicé una viga de madera de 15 × 10 mm, 280 mm de largo, tendida alrededor de mi costado, con lados uniformes. Por supuesto, es mejor usar una pequeña esquina de metal, pero no encontré una. En los bordes de la viga, teniendo en cuenta el ancho de la mesa de trabajo, taladré orificios de 4,1 mm para tornillos M4 × 25, en los que instalé arandelas con amplios campos desde la parte inferior de la viga para atraer la viga a la mesa de trabajo. Puse "tuercas" M4 en la parte superior del tornillo para un apriete conveniente.
Desde los extremos de la máquina, la abertura formada entre los bastidores, la base y la mesa de trabajo se cubrió con segmentos de tablero de fibra para evitar la dispersión de los productos cortados por toda la habitación. Por un lado, dejó la oportunidad de limpiar periódicamente el aserrín, colocando el panel de fibra en los tornillos, por otro lado, clavado con pequeños clavos.
Realmente ensambladora sin taladro eléctrico
Conclusión
En conclusión, me gustaría agregar que mi diseño está completamente desarrollado para los materiales y herramientas de trabajo que tenía. Cualquiera que tenga la oportunidad, puede hacer que la máquina sea completamente de metal, lo que solo agrega estabilidad a la máquina.
El trabajo de la máquina es suave con mínima vibración. Para mayor seguridad (como ya sabe, nunca es superflua) y protección contra movimientos accidentales, atraigo mi máquina herramienta con una abrazadera improvisada a la superficie de trabajo. La hoja de sierra va más allá del lado del escritorio de la máquina en 10 mm, lo cual es justo para mis necesidades de radioaficionado. La máquina a revoluciones medias de un taladro eléctrico corta fácilmente textolita con un grosor de 2 mm, tablero de fibra con un grosor de 5 mm, todavía no he probado otros materiales.
Bueno y lo más importante! Mantenga siempre las precauciones de seguridad y su manualidades te complacerá!